Introduction to Capacitors:
Types, Uses & More
Introduction
Capacitors are one of the most basic and important components in electronic circuits. For engineers who design circuits, accurate acquisition of knowledge about the characteristics and properties of capacitors is essential for product development.
However, if you think about the basic operation and mechanism of a capacitor again, you may notice that there are some things that are overlooked or misunderstood.
For young circuit design engineers, we present the "You Cannot Ask About Now. Introduction to Capacitors" covering everything from the basics of capacitors to today's hot topic of large-capacitance capacitors.
What is a capacitor?
What role do capacitors play in electronic circuits?
This chapter explains the basic structure of capacitors, how they work, and the units used to express the size of capacitors in design and development.
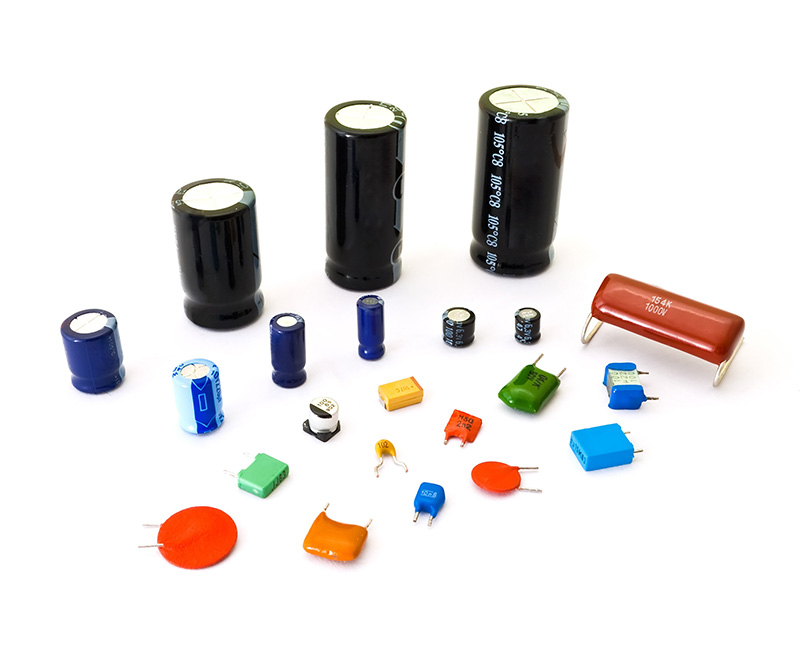
Is there a difference between a condenser and a capacitor?
There is no clearly defined difference between condensers and capacitors; both are electronic components that can physically store electric charges.
In English-speaking countries, it is called a capacitor because of its "capacity", but in Japan, it is said that it came to be called a "condenser" because it was translated as a "condenser (chikudenki)" because of its ability to condense electricity and store it.
Mechanism and function of capacitors
[ Structure ]
The circuit symbol used to represent a capacitor has two parallel lines drawn on it.
This indicates that the capacitor consists of two parallel conductor plate electrodes. For electrolytic capacitors with positive and negative polarities, the positive side may be marked with a + symbol. There are differences in notation methods among countries such as Japan (JIS), the United States (EIA), and Europe (EU, IEC).
The larger the area of the capacitor's electrode plates and the closer the distance between the two electrode plates, the higher is its ability to store electricity.
In addition, the electrode plates are electrically separated by an insulating material. This insulating material gives the capacitor the ability (capacity) to interrupt the DC current and store electricity. These materials are commonly referred to as dielectrics.
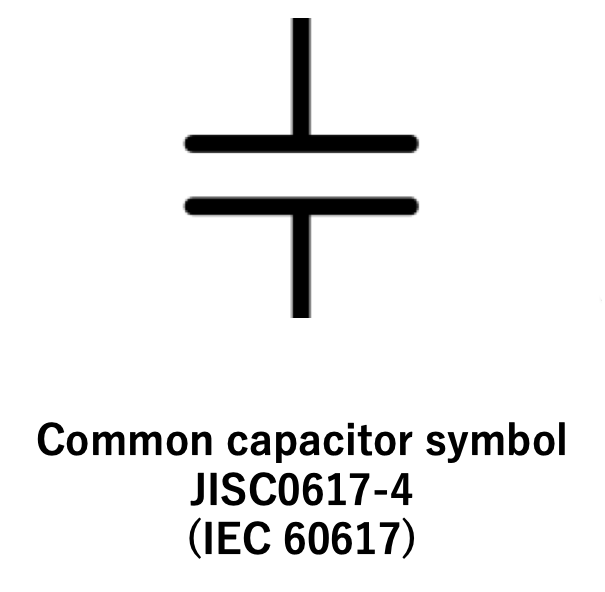
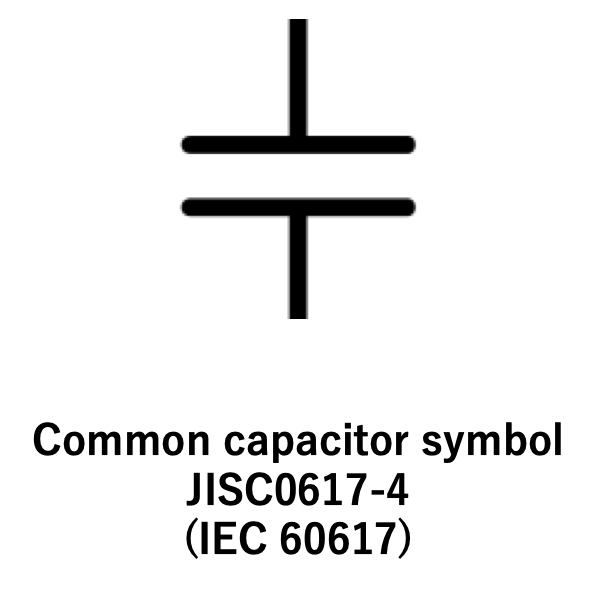
[ Ability and unit to store capacitance]
As shown in the figure below, when the switch is turned on and a DC voltage is applied to the capacitor, electricity (electric charge) instantly accumulates on the electrode plate (b). If the voltage is removed, the electric charge accumulated on the electrode remains intact. (c).
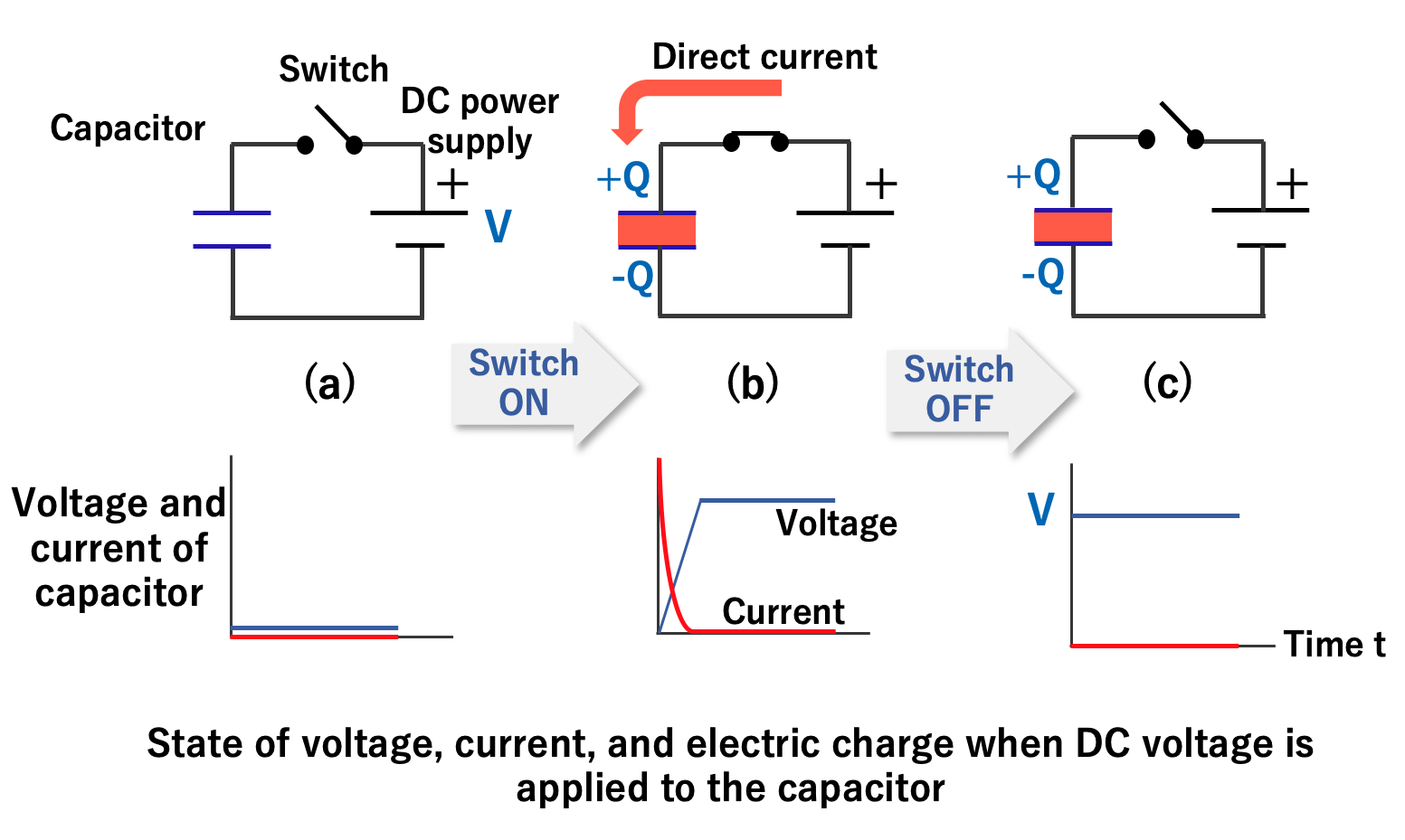
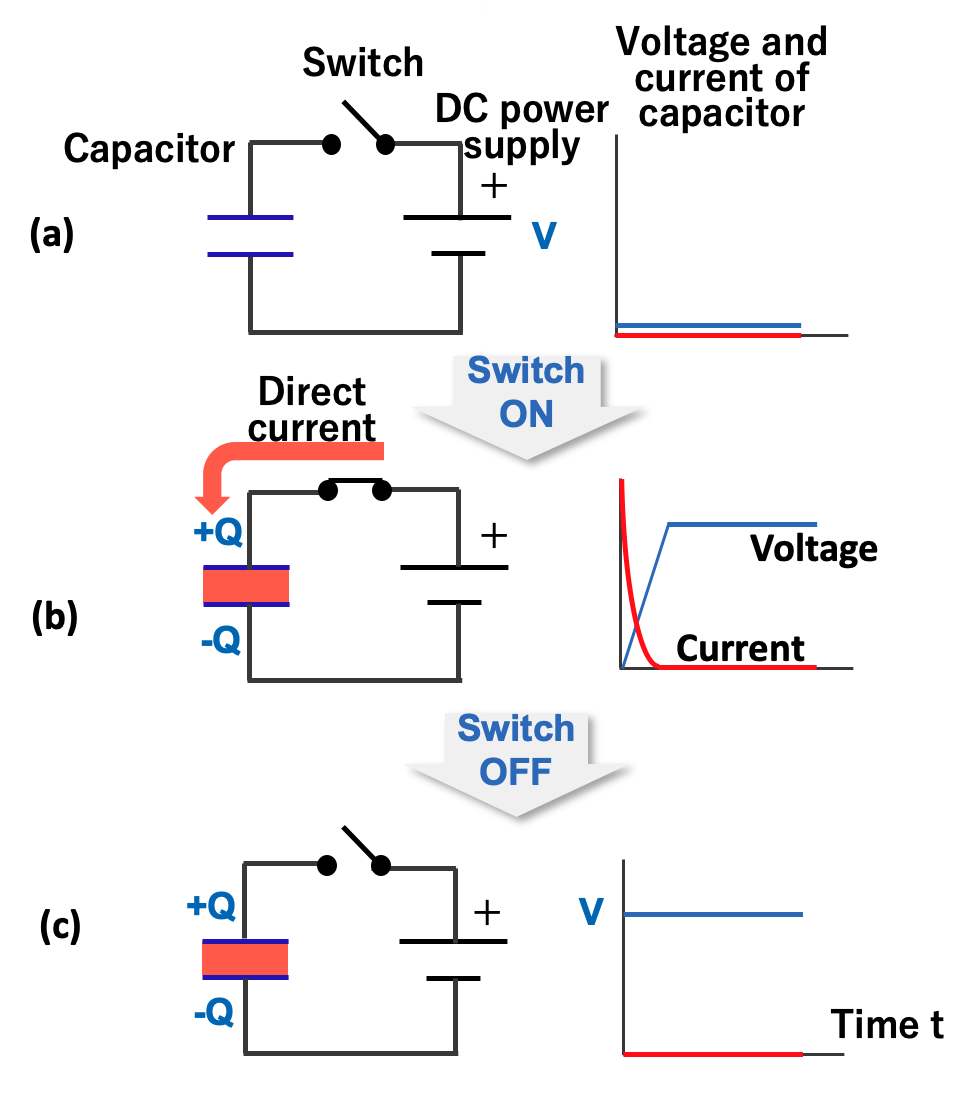
The ratio of the electric charge (Q) accumulated on the electrode to the applied voltage (V) is called the capacitance (C) of the capacitor. Capacitance is an index of the ability of an electrode to store an electric charge, and the unit called farad (abbreviated as F) is used in honor of the British physicist Michael Faraday. When a charge of one coulomb is stored on an electrode at a voltage of one volt, the capacitor is defined to have a capacitance of one farad.
[ Properties at DC and AC ]
As shown in the previous section, when a DC voltage is applied to a capacitor, an instantaneous electric charge accumulates on the electrode plate, and no further electric charge movement is possible.
In other words, the capacitor stops the DC current in an instant.
However, when an AC voltage is applied to the capacitor, the situation changes. This is because AC voltage is always switching between positive and negative voltage.
Initially, electric current flows like DC current, and an electric charge accumulates. However, when the voltage changes in the next instant, the accumulated electric charge is discharged. Then, the current flows in the opposite direction to the previous one to charge it.
In other words, charging and discharging are repeated in the capacitor according to the exchange of AC voltage, and it seems that electricity is flowing through it.
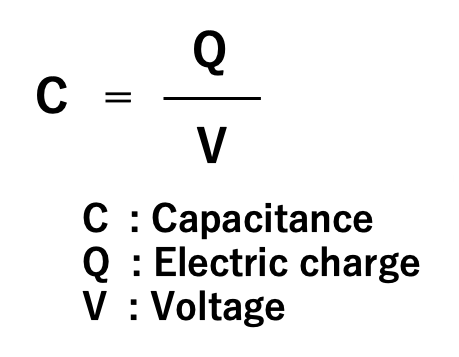
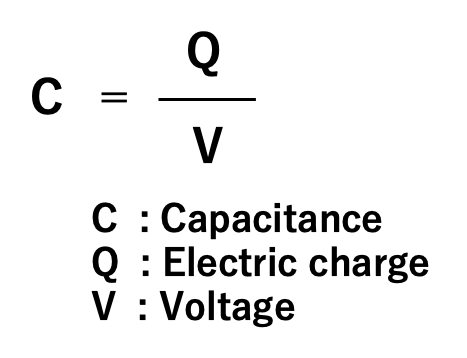
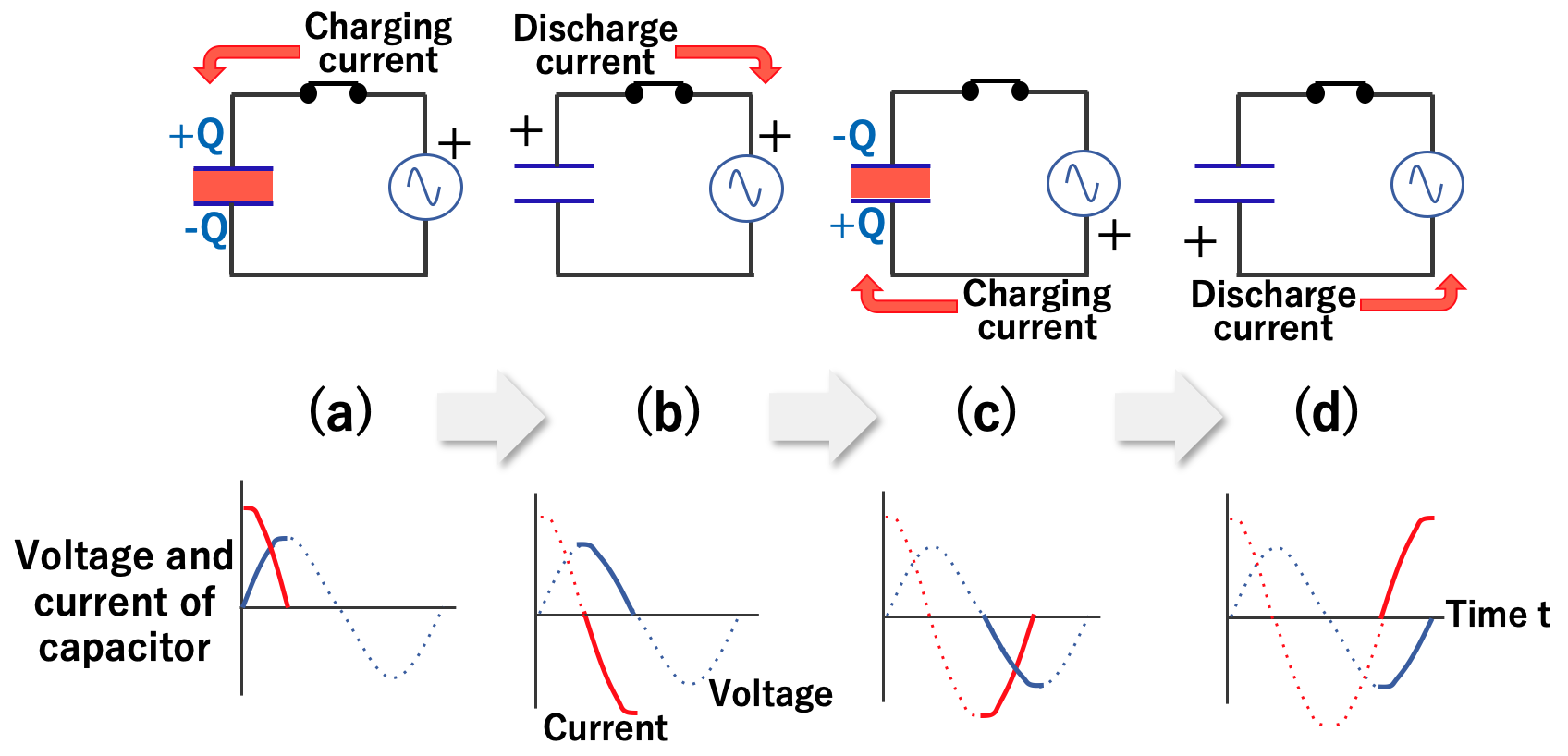
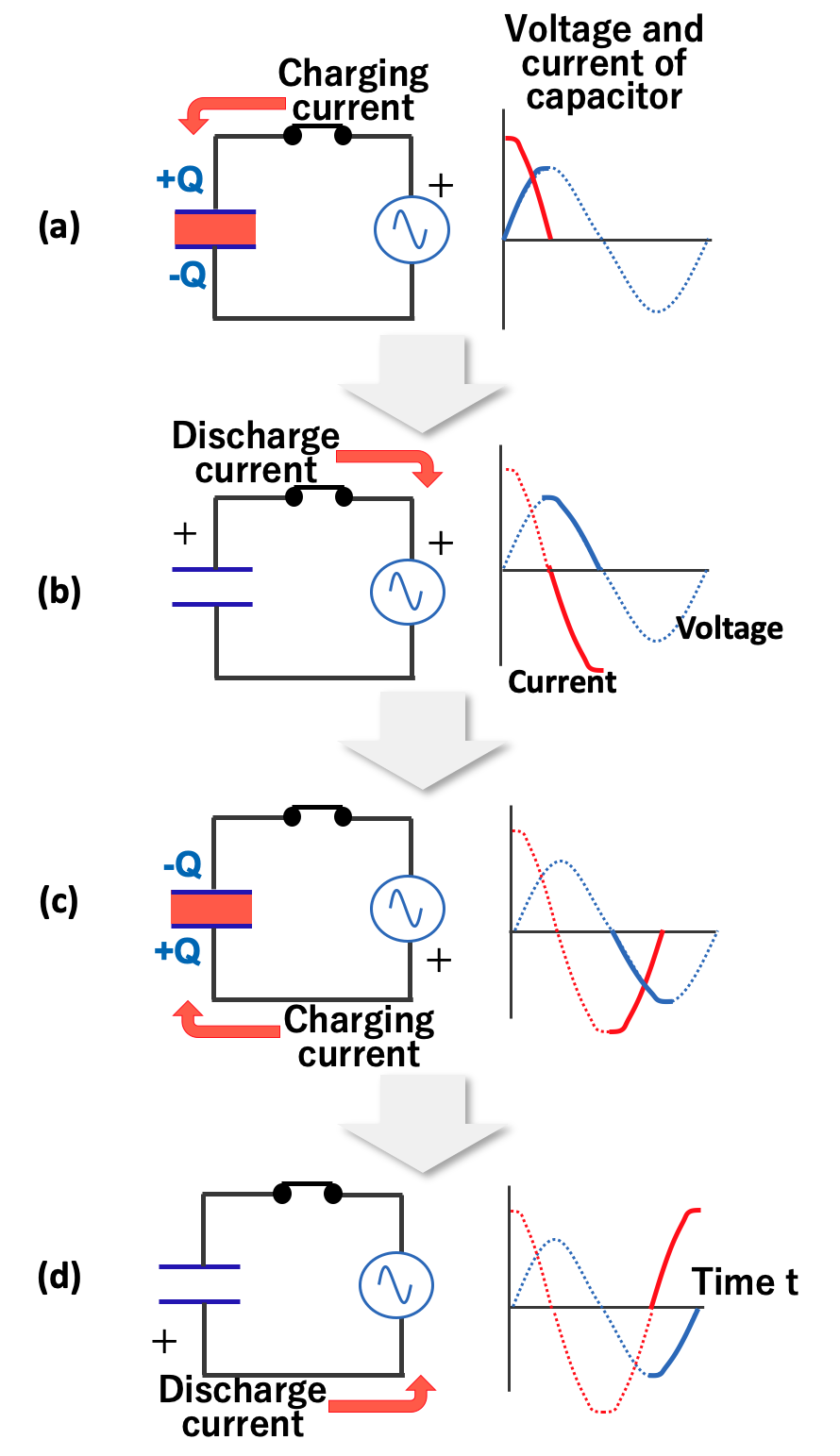
In summary, the functions of the capacitor are the following two:
① Stores the electrical energy, and give this energy again to the circuit when necessary.
② Blocks the DC current flow, and permits the AC current flow.
Also, the faster the alternating current voltage is switched (called alternating current with higher frequency), the easier it is for the capacitor to pass the alternating current.
[ How capacitors work ]
Because of the above functions, capacitors perform two major functions in electronic circuits:
① In DC current, electricity is stored and discharged.
Capacitors not only store electric charge but also discharge it, so the capacitor itself becomes the power source. A simple example is the strobe light emission of a camera. The camera stores an electric charge in a capacitor built into the camera and discharges it all at once to create an intense flash.
② Create a clean direct current (remove AC components)
Using the function whereby the capacitor allows alternating current to pass through, it is possible to turn an unstable direct current with a wave-like component into a clean direct current.

As shown in the figure, if a capacitor is connected between the input and output sides and connected to the ground, the AC component will flow to the capacitor and only the direct current will flow to the output circuit. It is also possible to output a stable voltage even if there is a large voltage wave at the input.
Capacitors in a circuit have a simple but very important function. Our capacitors are characterized by their small size, large capacitance, high withstand voltage, and long life. We will explain in detail how to use these characteristics in the next issue.
Basic Properties of Capacitors
Capacitors store electric charge and block direct current
A capacitor is a device that stores electrostatic energy by accumulating electric charges on two closely spaced surfaces that are insulated from each other. A real capacitor is composed of an insulator sandwiched between two electrodes (Fig.1) .
When an insulator is placed between the electrodes of a parallel plate capacitor and a voltage V is applied, the insulator is exposed to the electric field E between the electrodes. Although the insulator blocks DC electric current to flow, the electric field causes the atoms of the insulator to split into positively charged and negatively charged parts*01 (Fig.2). In other words, an external electric field E (=V/d) induces an opposite induced electric field E’ in the insulator, and electrical energy is stored. This phenomenon is called dielectric polarization, and the material that causes dielectric polarization is called a dielectric.
*01 AIC Web-site: https://www.aictech-inc.com/information/capacitor_foundation03.html
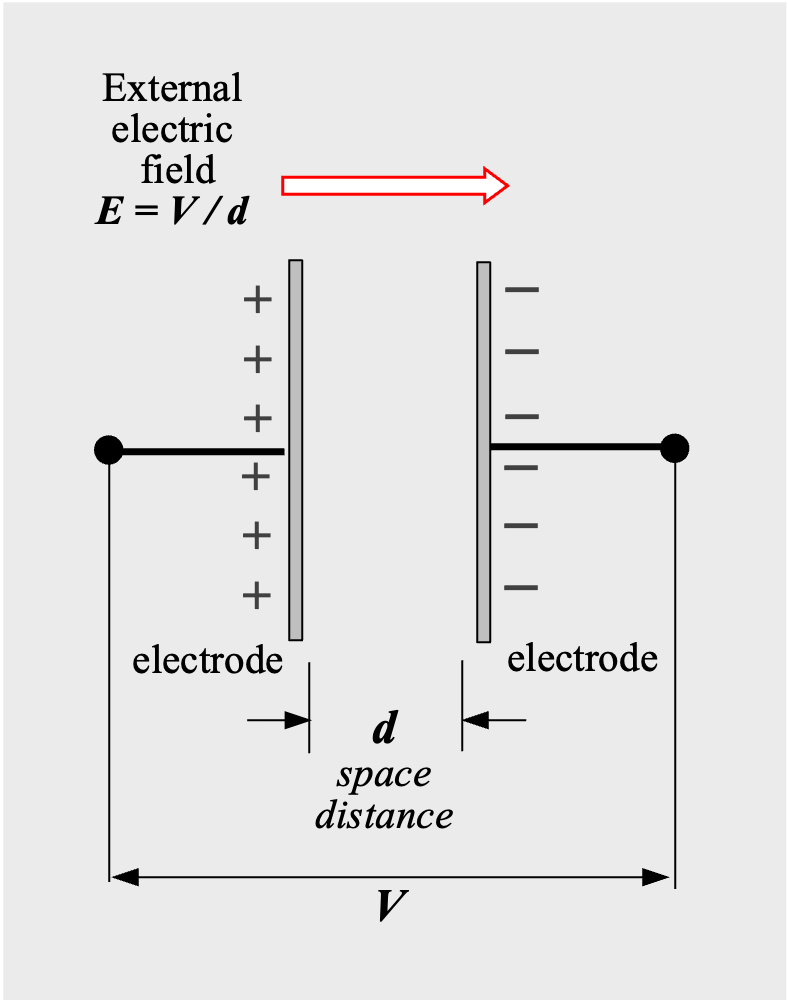
Electric charges on electrodes
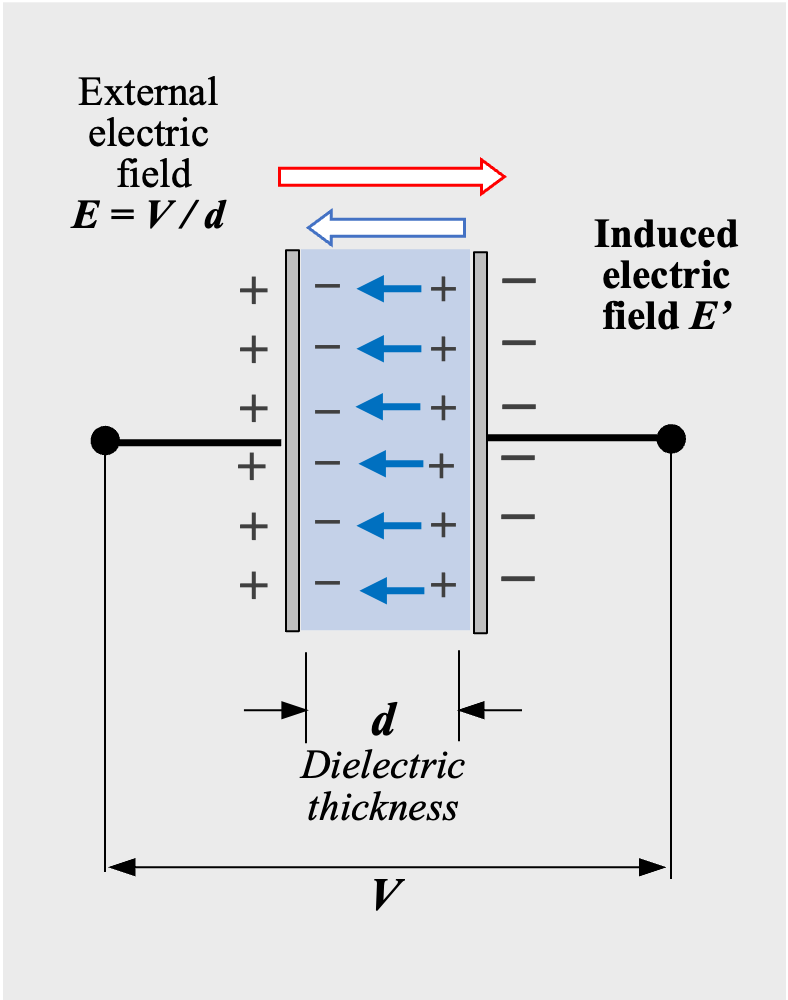
Electric charges on electrodes and in dielectric
As shown in Fig.3, the DC current flowing into a capacitor gets smaller over time. That is, initially, a large current flows into the capacitor instantaneously (charging current), and charge is stored in the electrodes. Subsequently, a current that polarizes the dielectric (absorption current) flows, causing dielectric polarization. Finally, when the capacitor is fully charged, no DC current flows *02 .
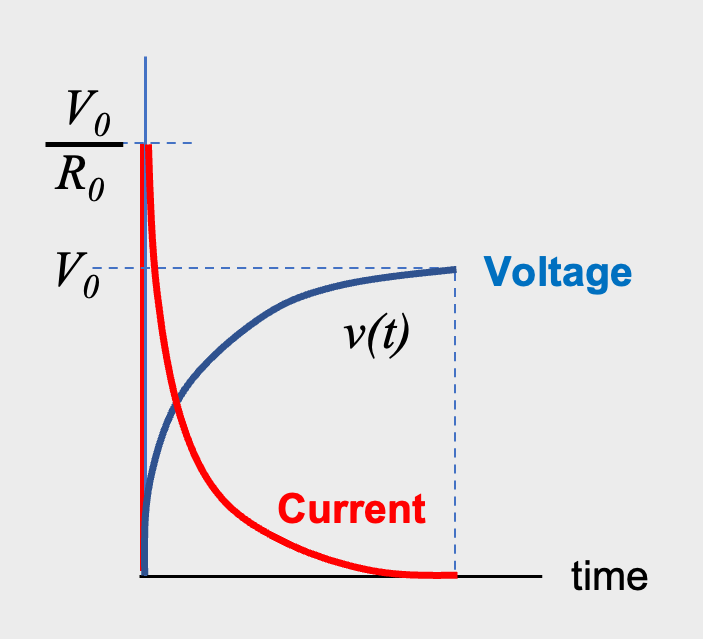
Capacitor voltage and current v.s. time
*02 AIC Web-site: https://www.aictech-inc.com/information/capacitor_foundation05.html
Capacitors allow alternating current flow
AC current flow periodically switches between positive and negative voltage. At first, the current flows from the positive pole of the power supply and charges the capacitor, just like direct current. When the voltage of the capacitor reaches the power supply voltage, V, the current goes to zero (Fig.4). As the power supply voltage drops toward zero, the capacitor discharges and current flows in the reverse direction (Fig.5).
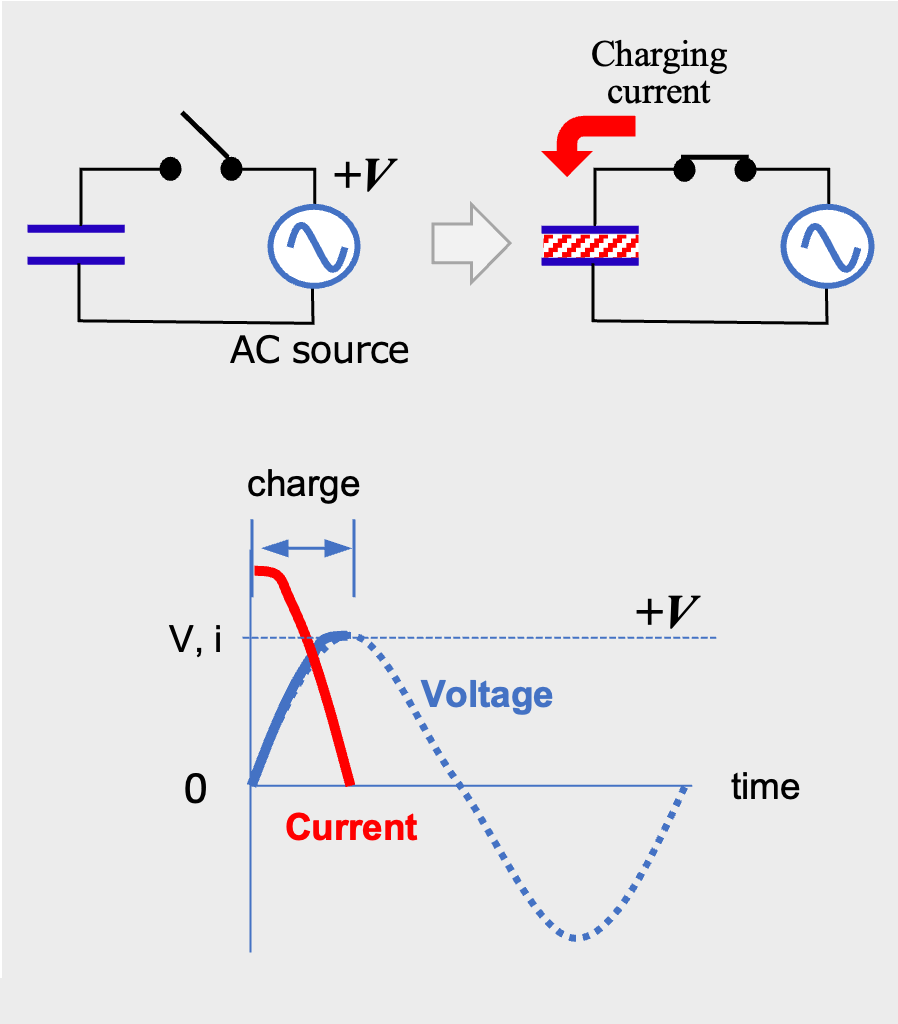
AC current flow through a capacitor (charging phase)
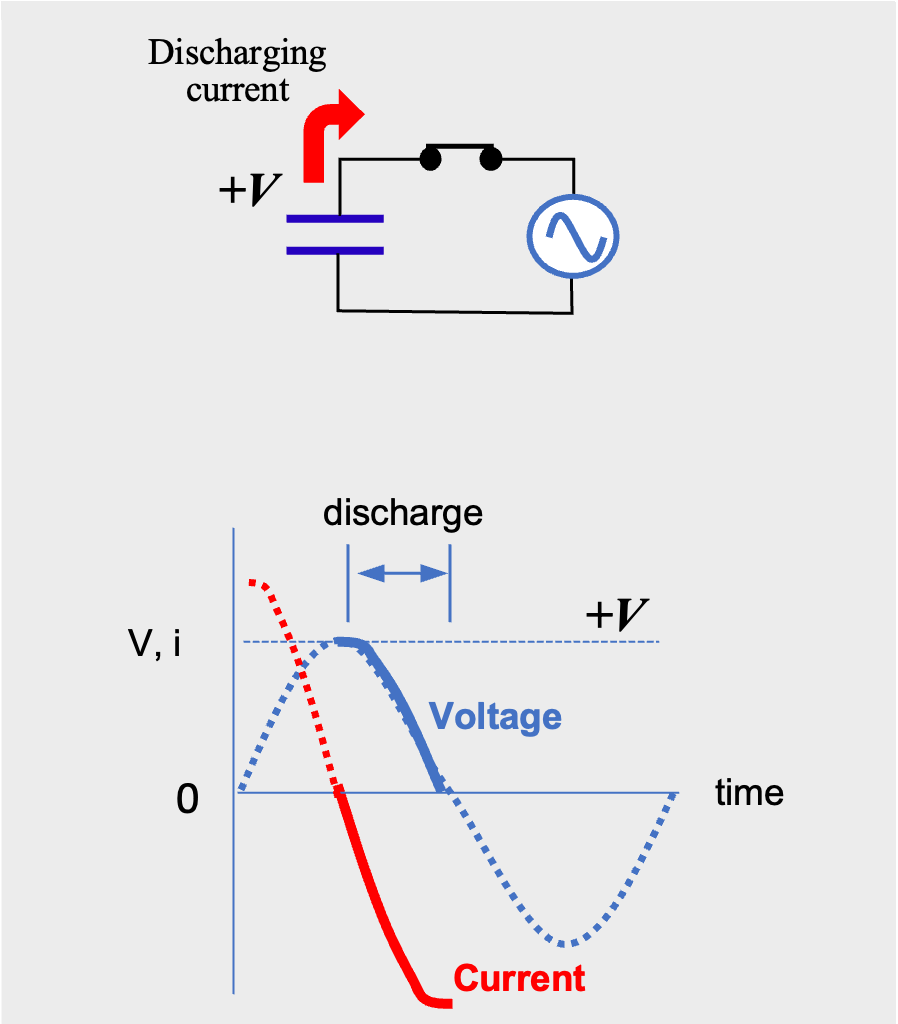
AC current flow through a capacitor (discharging phase)
When the voltage reverses, the capacitor begins charging again, and the charging continues until the voltage reaches the opposite peak (Fig.6). Then, when the voltage tends toward zero, the capacitor begins to discharge and current flows in the opposite direction (Fig.7). In other words, in AC, the capacitor charges and discharges repeatedly as the voltage changes, and the capacitor behaves as if it made pass through AC current.
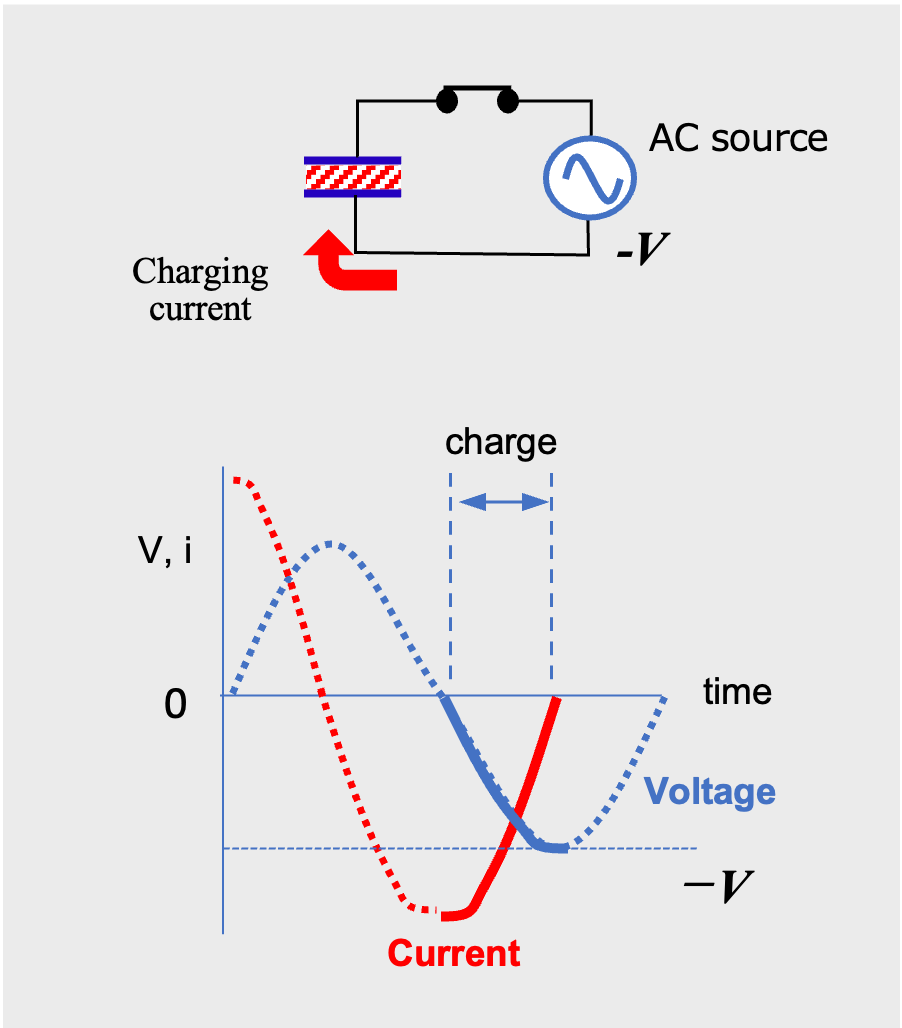
AC current flow through a capacitor (reverse charging phase)
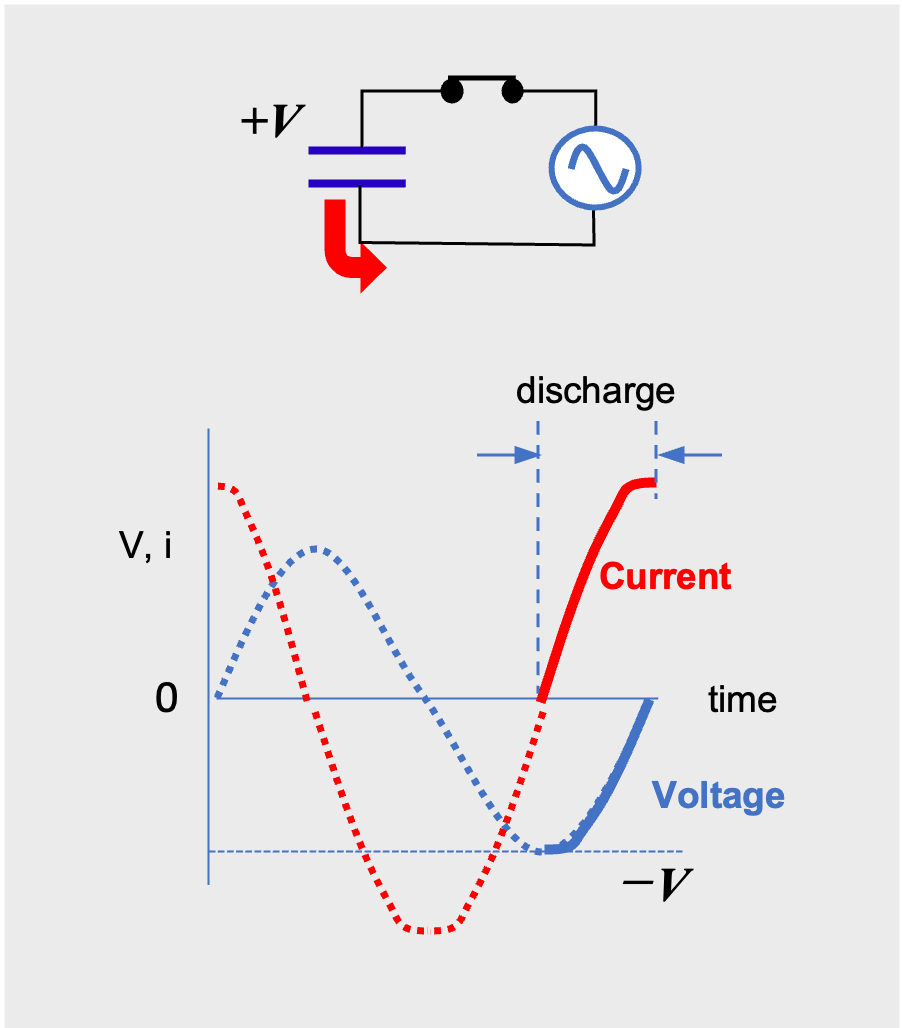
AC current flow through a capacitor (reverse discharging phase)
Capacitance is the ability to store an electric charge.
The charge Q on a capacitor is proportional to the applied voltage V. Its proportionality constant is defined as capacitance C by Equation (01). In other words, capacitance is a physical quantity that expresses the ability of a capacitor to store an electric charge at an applied voltage.

Capacitance C is expressed by Equation (02) using permittivity of free space ε0 (8.854×10-12 [F/m]) , relative permittivity εr , area of electrodes A, and distance d between electrodes. Equation (02) indicates that the capacitance can be increased by using a dielectric with a large εr . Table 1 shows the relative dielectric constants of major dielectrics used in capacitors.

Dielectric withstanding voltage
The upper limit of the voltage that a capacitor can tolerate depends on the physical properties of the dielectric. That is, if excessive voltage is applied to the capacitor, the dielectric will not be able to block the DC current. This applied voltage is known as the breakdown voltage (VBD ) and is the product of the distance between the capacitor plates (d) and the dielectric strength (EDS ) *03 Equation (03) .
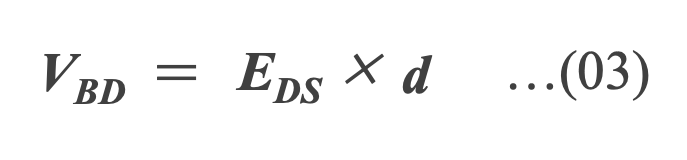
*03 F. T. Ulaby, Fundamentals of Applied Electromagnetics. Prentice Hall, 2007. [36]
As shown in Equation (02) and (03), VBD is proportional to d, while the capacitance is inversely proportional to d. Therefore, as the dielectric thickness increases, the maximum operation voltage increases, but the capacitance decreases. To obtain a large capacitance, the electrode area A must be increased by using a dielectric with a large relative permittivity εr . Needless to say, this increases the physical size and hence the cost of the capacitor. In real capacitors, various techniques and innovations are applied to economically and physically balance the trade-off between withstand voltage and capacitance.
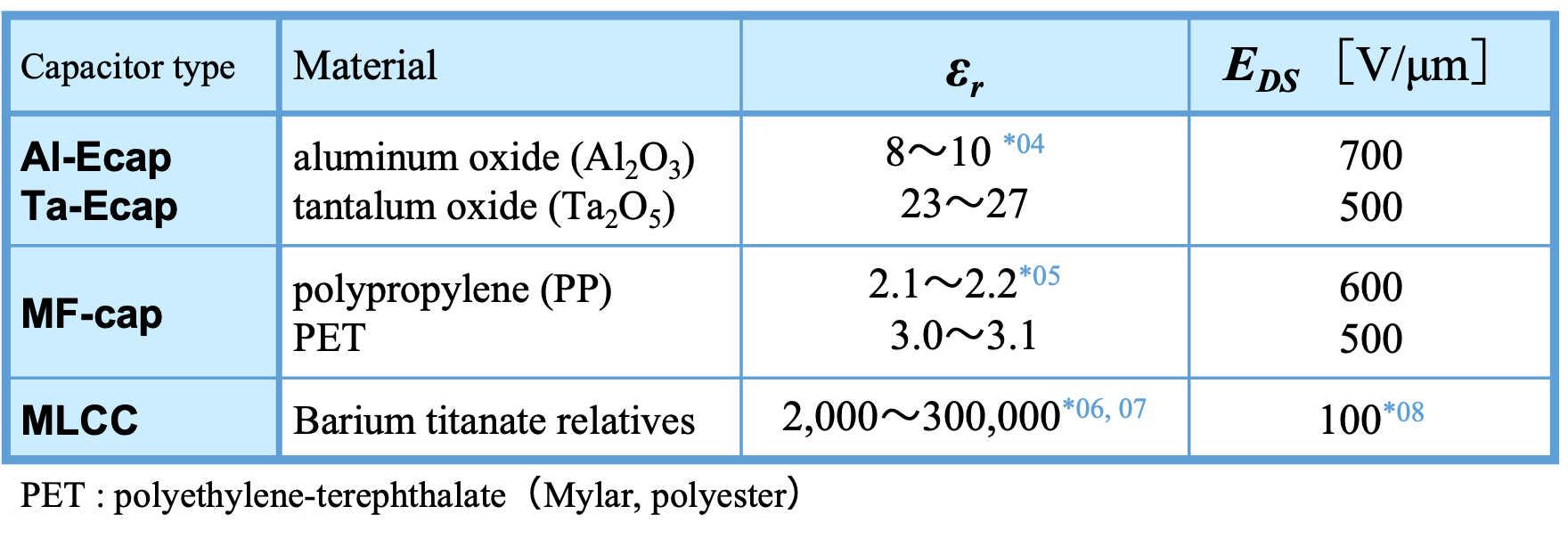
*04 https://www.jstage.jst.go.jp/article/sfj/72/4/72_216/_pdf
*05 https://www.nature.com/articles/pj198470.pdf
*06 A. J. Moulson and J. M. Herbert, Electroceramics: Materials, Properties, Applications. John Wiley & Sons Inc, Jul. 2003. [32]
*07 T. Lebey, et al., “Origin of the colossal permittivity and possible applications of cct ceramics," in 55th Electronic Components and Technology Conference, 2005 (ECTC), 2005, pp. 1248-1253. [34]
*08 M. H. Yeh, Y. et al., “Electrical characteristics of barium titanate films prepared by laser ablation," Journal of Applied Physics, vol. 74, no. 3, pp. 2143{2145, 1993. [33]
The EDS value in Table 1 is as an ideal parallel-plate capacitor. However, real capacitor electrodes are not parallel plates, and dielectric breakdown occurs at sharp angles or points on the electrode surface rather than over the entire surface. Once the dielectric breaks down locally, the breakdown rapidly propagates from electrode to electrode, degrading the dielectric insulation and short-circuiting the capacitor*09.
Also, if a dielectric is stressed under very high electric field, the dielectric atoms ionize and the dielectric is destroyed *10. Furthermore, impurities and/or inhomogeneities in the dielectric can make the current flow more easily, and the dielectric can be destroyed at a lower voltage than the theoretical EDS value. If the dielectric is crystalline, the ionized atoms and free electrons by the high voltage can ionize other dielectric atoms, causing avalanche ionization*11.
*09 P. Scherz, Practical Electronics for Inventors. McGraw-Hill/Tab Electronics, Nov. 2006. [38]
*10 Intrinsic breakdown
*11 When excess conduction electrons flow through a solid with kinetic energy above a certain value, electron avalanche occurs, eventually breaking the bonds between the solids.
Dielectric properties dominate capacitor performance
The dielectric properties are major factor that characterize the performance of capacitors. Fig.8 presents the relative permittivity, continuous operational field strength and energy density limits of Al2O3, polypropylene and ceramics, which are the dielectric materials used in Al-Cap, MF-Cap and MLCC, respectively *12 . The theoretical limit is in the range of 10 J/cm3 and the commercial available one is about 2 J/cm3.
Al2O3 , the dielectric of Al-Ecap, has the highest energy density with high electric field strength and large dielectric constant. Ceramics may have a much higher dielectric constant than Al2O3 or plastic films, but they have a lower electric field strength, resulting in a volumetric energy density similar to that of film.
*12 M. Marz, A. Schletz, B. Eckardt, S. Egelkraut, and H. Rauh, “Power electronics system integration for electric and hybrid vehicles,” in Proc. Int. CIPS, 2010, pp. 1–10.
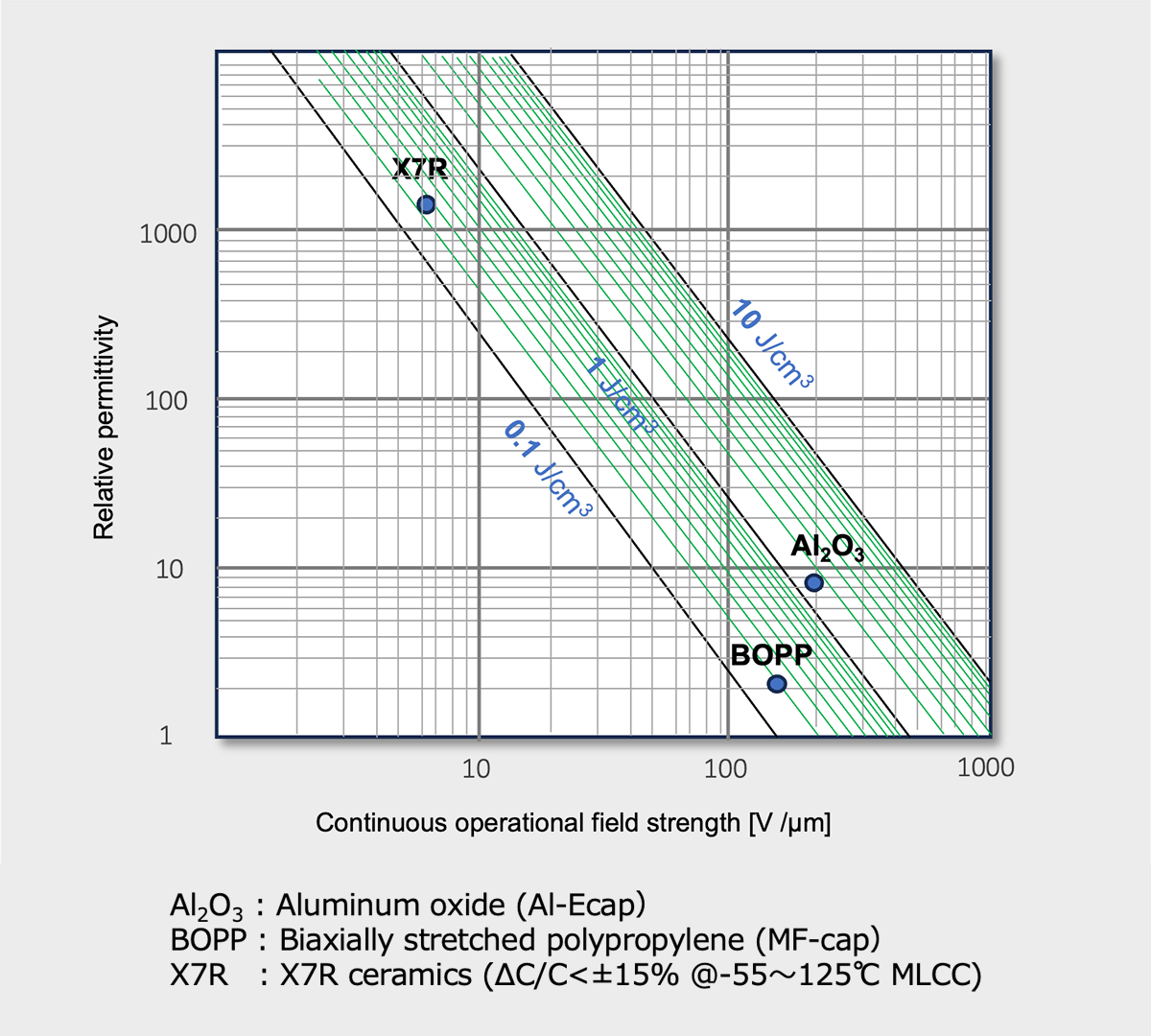
Relative permittivity, continuous operational field strength and energy density limits of various dielectric
Real capacitors have resistance and inductance.
An ideal capacitor has only capacitance; stored energy does not leak out of the capacitor and the charged energy is released without loss. In a real capacitor, however, there is not only pure capacitance C consisting of electrodes and dielectric, but also capacitance other than dielectric, resistance, and inductance. Also, since the dielectric is not a perfect insulator, a small leakage current (Ileak ) flows from the anode to the cathode during charging. In an equivalent circuit, the leakage current is represented by a resistance Rp connected in parallel to the dielectric capacitance (C). The dielectric also has a dielectric absorption Cd and a dielectric loss Rd due to molecular polarization*13. In addition, there is an equivalent series resistance (ESR) due to the resistive component connected in series with the capacitance C, and an equivalent series inductance (ESL) is parasitic on the external terminals and internal lead tabs (Fig. 12).
In capacitor applications, it is necessary to know in advance that the various parameters of real capacitors will change under temperature, voltage, frequency, time, etc. This is because a more positive lifetime estimation is possible by taking into account the variation of each parameter with conditions.
*13 B. W. Williams, Principles and Elements of Power Electronics: Devices, Drivers, Applications, Passive Components. Glasgow, U.K.: Univ. Strathclyde, 2006, ch. 26. [4]
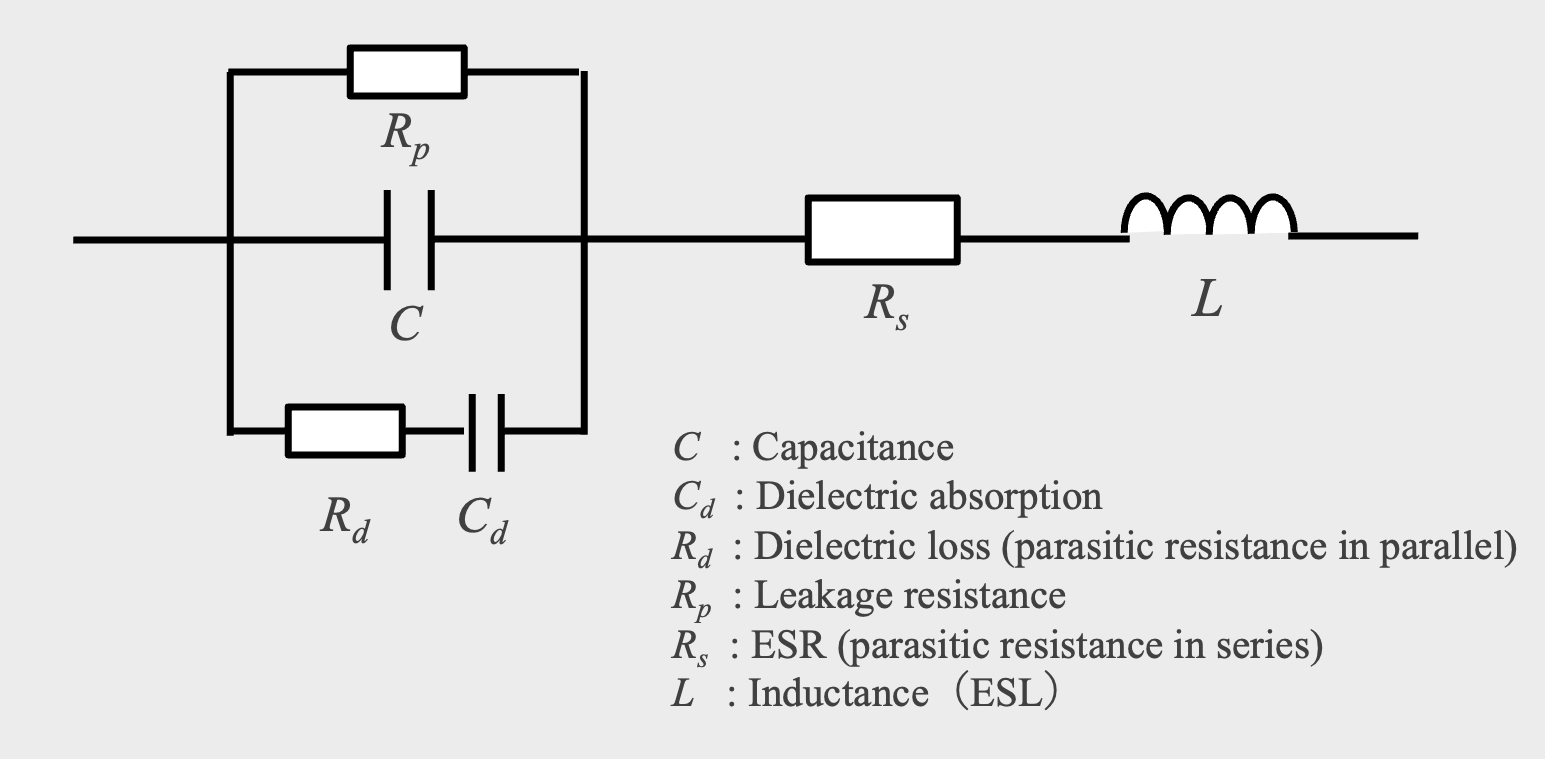
Equivalent circuit diagram of capacitor
Types of capacitors
Although the basic role is the same, there are various types of capacitors depending on their application and size. This chapter explains the different types of capacitors and their respective characteristics.
Major Capacitor Types and Features
Major capacitor types
Table 2 shows the overview and features of typical capacitor types. Capacitor types are classified by dielectric material, and as mentioned above, the dielectric has a significant impact on capacitance range, withstanding voltage, and other capacitor performance. However, even if the dielectric is the same, capacitors with different types of electrodes and element forms have different characteristics*14.
*14 AIC Web-site: https://www.aictech-inc.com/information/capacitor_foundation03.html
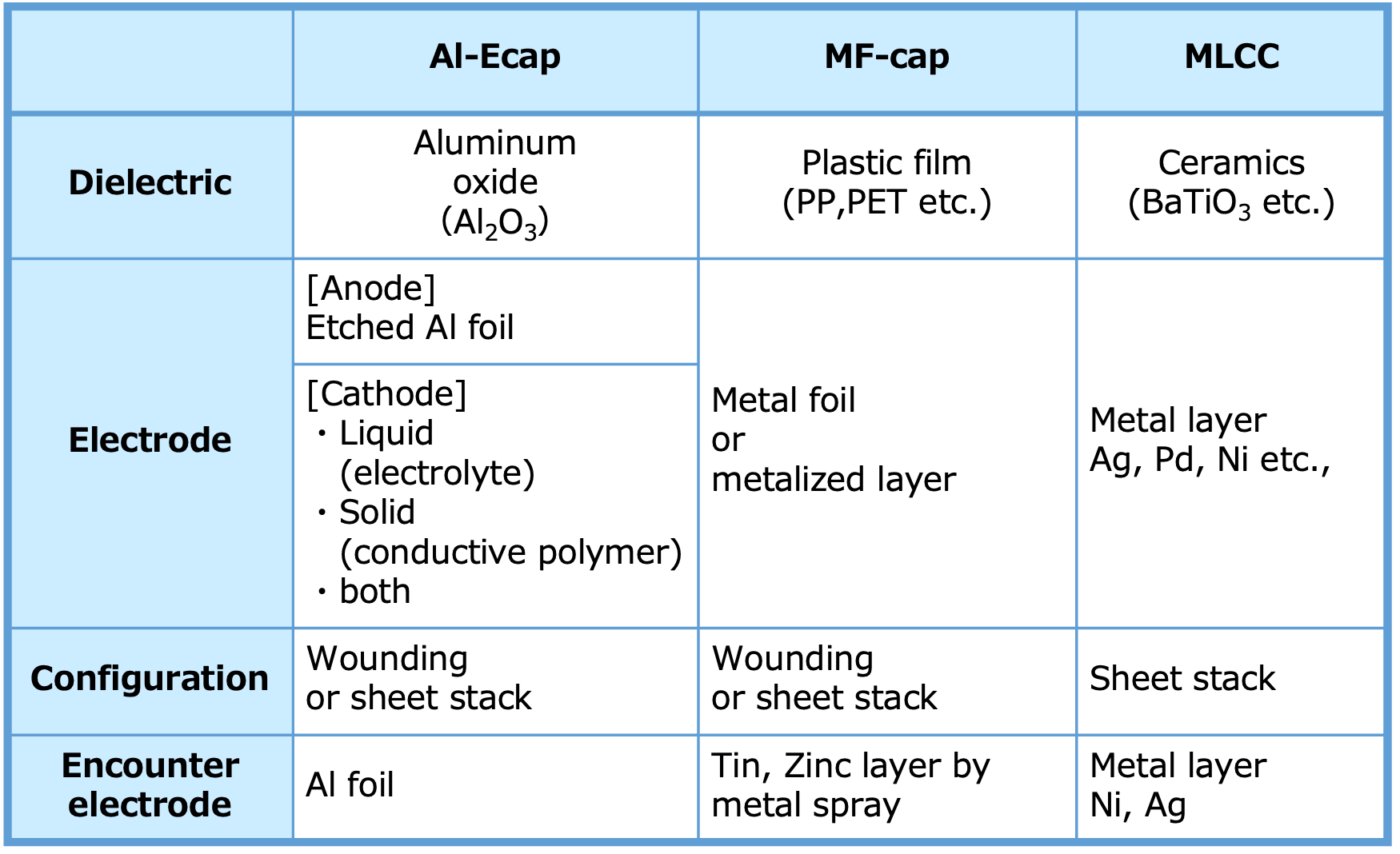
Rated voltage and capacitance range
Fig.10 shows the range of capacitance and voltage rating covered by typical capacitors. Capacitors cover an extremely wide range of capacitance, from pico-Farad (pF, 10-12 Farad) to over 1 Farad (F). However, the range varies with the type of capacitor. In general, Al-Ecap covers the large capacitance range, but in recent years, MLCCs and MF-caps with large capacitance have been launched.
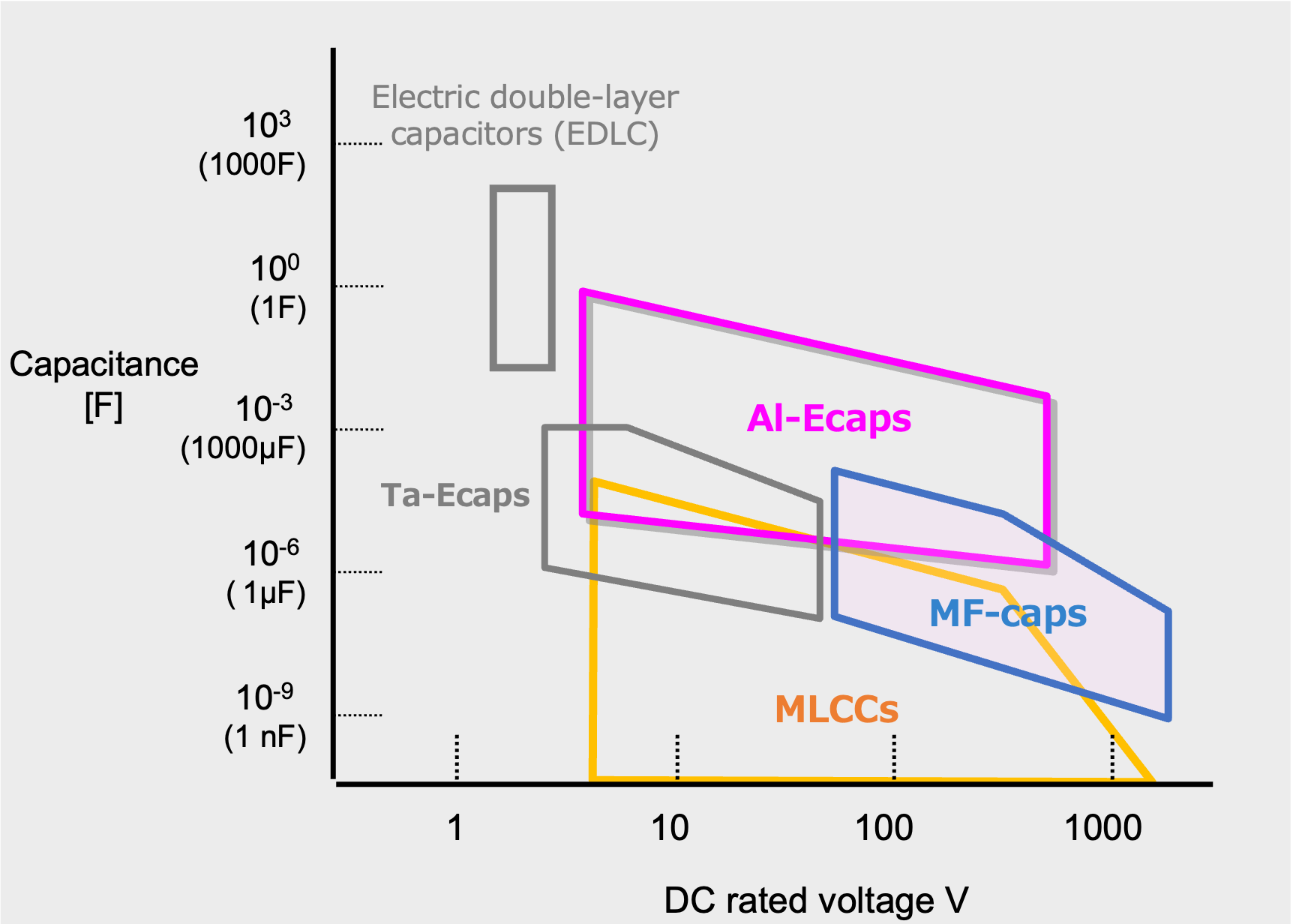
Range of capacitance and voltage rating covered by typical capacitors
The voltages range which a capacitor could cover depends on the capacitor type. Since the withstand voltage of a capacitor is affected not only by the type and thickness of the dielectric, but also by the material and structure of the electrodes, capacitor engineers conduct high-temperature load tests, evaluate insulation resistance, breakdown voltage, and electrical characteristics, and design voltage ratings based on these results. The larger the margin between the voltage at which the capacitor is actually applied and the rated voltage, the higher the reliability. Equipment that requires higher reliability is often mandated to use a margin of 50% or less, and higher reliability can be achieved by using a margin of 50% or less.
Capacitor choice by application
In capacitor applications, the appropriate capacitor is chosen for the various functions and roles in the circuit. For example, the photoflash capacitor is used to store a large amount of energy, which can be released nearly instantaneously to power a xenon bulb, providing the light necessary for flash photography. In this allocation, small sized AL-Ecaps are generally referred to as photoflash or strobe capacitors and several hundred microfarads with 300~450V rated voltages. On the other hand, Al-Ecap has a limited lifetime and larger ESR than other capacitors. Also, operational temperature range is relatively limited. For this reason, Al-Ecap is not chosen for high-frequency filter circuits or applications where large ripple currents flow. In other words, there is a territory among capacitors by application as shown in Fig.11
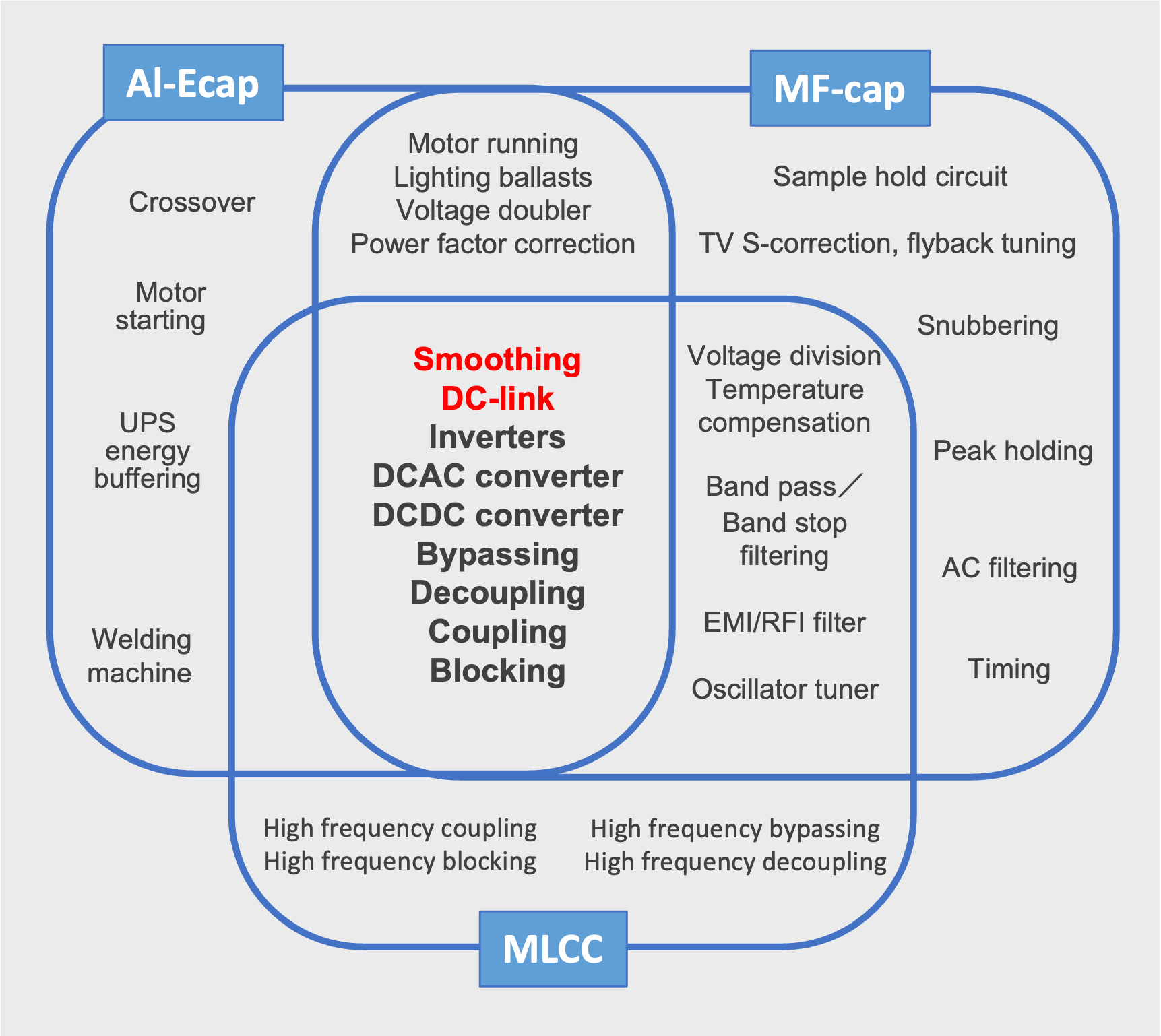
Typical applications of Al-cap、MF-cap、MLCC and territories
Aluminum electrolytic capacitors
A capacitor that forms a dielectric oxide film on the surface of an aluminum foil that serves as the anode and uses an electrolyte or a conductive polymer, etc. as the cathode is called an aluminum electrolytic capacitor.
Many of them have a cylindrical shape and are so common that many people think of this shape when they think of capacitors. Compared to other types of capacitors, electrolytic capacitors have the major characteristic of being able to store a large amount of electricity even though they are the same size as other capacitors. While most capacitors are made for digital circuits with a diameter of 10 mm or less, we sell products for power electronics circuits with a volume of 0.5 to 1 liter.
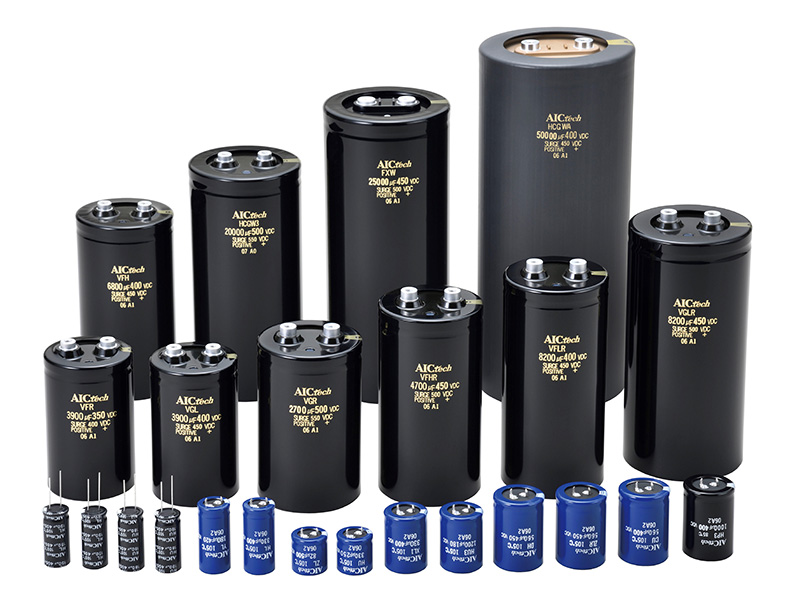
Aluminum electrolytic capacitors use an electrolytic solution filled in paper (separator), which has the disadvantage that the electrolytic solution evaporates with age and the performance deteriorates. They are consumable parts that need to be replaced periodically.
AIC tech aluminum electrolytic capacitors
AIC tech Inc. offers a comprehensive range of aluminum electrolytic capacitors, each tailored to meet specific application requirements:
Screw Terminal Type: These capacitors are designed for high-reliability applications, featuring long life spans and the ability to handle high ripple currents. They are suitable for use in power supplies, inverters, and other industrial equipment.
Snap Mount Type: Engineered for easy PCB mounting, these capacitors provide excellent durability and performance in power electronics. They operate within a wide temperature range and are ideal for applications requiring high ripple current capability.
Radial Type: These capacitors are designed for standard applications with excellent reliability. They feature a useful life of up to 5,000 hours and an operating temperature range from -25 to +105°C.
Each type is available in various series, offering a range of operating voltages, capacitance values, and specialized features to accommodate diverse electronic applications.
Film capacitors
A film capacitor is a capacitor that uses plastic film as the dielectric. Compared to aluminum electrolytic capacitors, the amount of electricity stored in these capacitors is more stable at both high and low temperatures, and they can withstand higher voltages and have a longer service life.
Since the film is wound into a cylindrical shape to make the element, most of the products with large capacitance are cylindrical in shape, but square products are also made for small and medium capacity products. We have both types available.
For the film that becomes the dielectric, materials such as polypropylene used for food containers, syringes, DVD cases, etc., clothing fibers such as fleece, and PET (polyethylene terephthalate) used for beverage bottles are used. Since these materials have the ability to store electricity (permittivity), which is only about 1/4 that of aluminum electrolytic capacitors, in order to store more electricity, a large amount of film is required, resulting in a larger capacitor size.
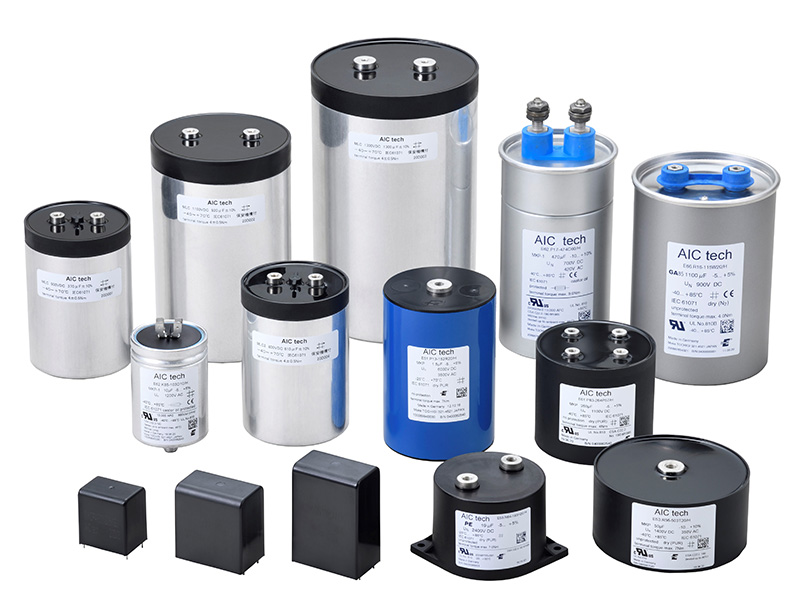
AIC tech plastic film capacitors
AIC tech Inc. offers a comprehensive range of plastic film capacitors, specifically designed to meet the demands of power electronics applications. These capacitors are categorized into several series, each tailored to specific operational requirements:
MLC Series: Standard DC capacitors encased in aluminum, operating within a temperature range of -40°C to +85°C. They offer rated voltages between 900V and 1,500V, with capacitance values ranging from 70µF to 2,300µF.
MLC2 Series: Designed for applications requiring larger capacitance, these aluminum-encased DC capacitors also operate from -40°C to +85°C. They support rated voltages of 800V and 900V, with capacitance ranging from 230µF to 3,800µF.
MLCA Series: These capacitors are optimized for high ripple current applications, featuring aluminum enclosures and operating temperatures between -40°C and +85°C. They accommodate rated voltages from 600V to 2,200V and capacitance values between 90µF and 5,000µF.
MKCP4 Series: Standard DC capacitors with a resin-encased design, suitable for temperatures from -40°C to +85°C
Ceramic capacitors
A capacitor that uses ceramic (pottery) as its dielectric is a ceramic capacitor. By changing the composition of raw materials, it is possible to create dielectrics with various performances.
The electrodes are not rolled up like aluminum electrolytic capacitors or film capacitors but are fabricated by layering multiple layers of a compounded slurry-like ceramic material and paste-like electrode material. For this reason, small capacitors with a size of a few millimeters or less are generally used, and they play an active role in digital circuits. A single smartphone uses 800 to 1,000 ceramic capacitors, and the production quantity is the largest production volume among the capacitors.
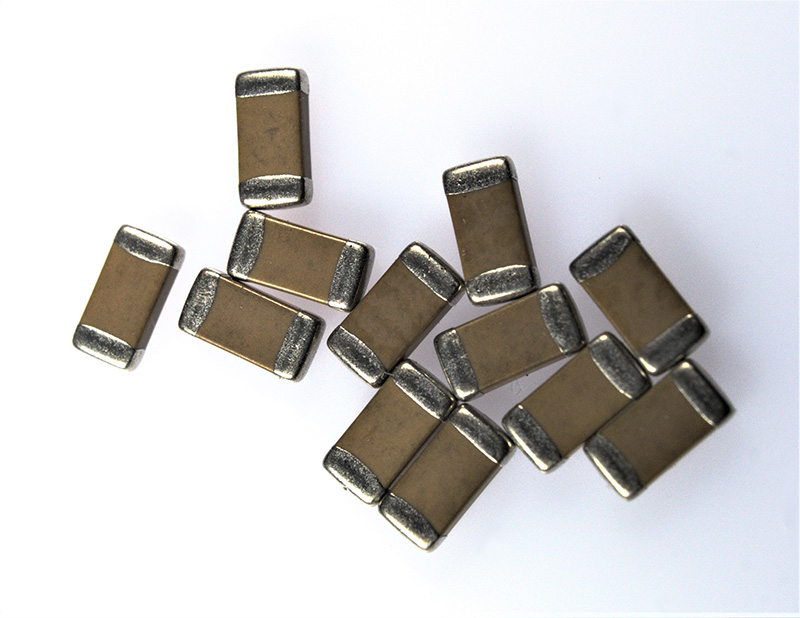
Electric double-layer capacitors (EDLC)
An electric double-layer capacitor has an extremely large capacitance compared to other capacitors. There is no dielectric in this capacitor, and a lot of electric charge can be stored in the area called the electric double layer, which is created between the activated carbon of the electrode and the electrolyte solution.
Since there is no dielectric to serve as the insulator as in other capacitors, the withstand voltage is low, and it is used as a power source like a battery rather than an electric circuit. Compared to rechargeable batteries, such as lithium-ion batteries, its characteristic is that the charging time is short.
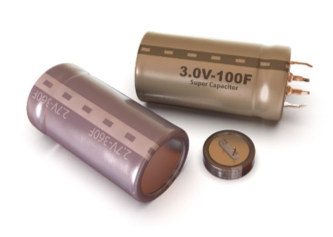
Capacitor comparison
Selecting the appropriate capacitor type is crucial in power electronics, as it directly influences the performance, efficiency, and longevity of electronic systems. Each capacitor type—aluminum electrolytic, film, and ceramic—offers distinct characteristics that make them suitable for specific applications.
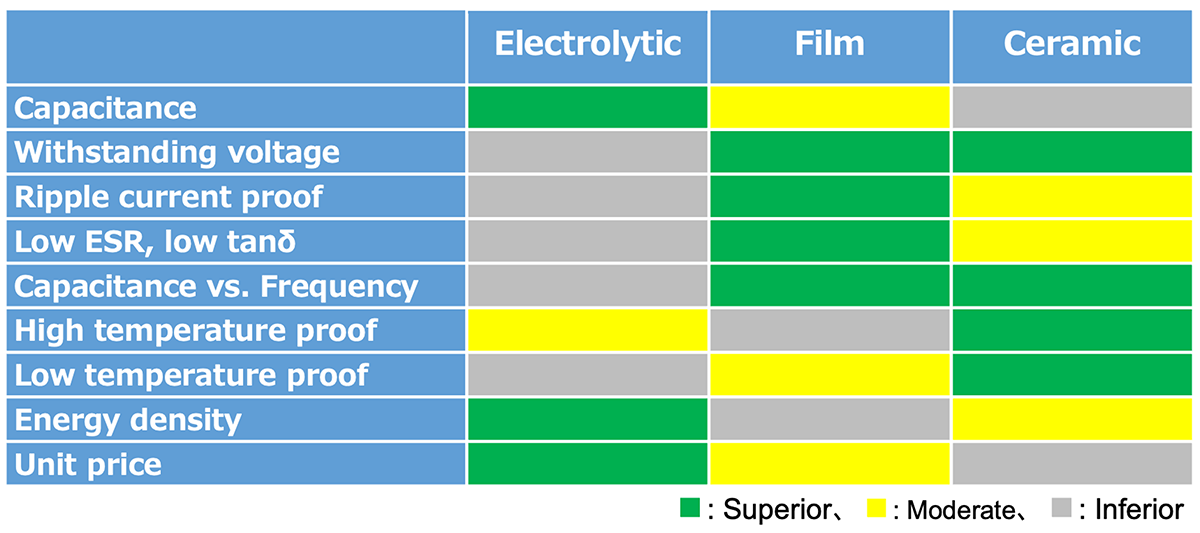
The table above summarizes the key characteristics of aluminum electrolytic, film, and ceramic capacitors, comparing parameters such as capacitance range, voltage rating, equivalent series resistance (ESR), high and low-temperature performance, energy density, and unit price. By presenting the strengths and limitations of each type, this table provides a clear reference for selecting the most suitable capacitor for specific applications.
Capacitor Selection Guide
Key points to consider when choosing between aluminum electrolytic and film capacitors include:
Voltage Rating: Film capacitors handle higher voltages (up to several kV), while aluminum electrolytic capacitors are limited to around 600–700V.
Capacitance Stability: Film capacitors exhibit low capacitance variation with temperature and frequency, whereas aluminum electrolytic capacitors are more susceptible to changes.
Energy Density: Aluminum electrolytic capacitors offer higher energy density and are more compact, making them ideal for space-limited designs.
Ripple Current Handling: Film capacitors excel in ripple current rejection with low ESR, while aluminum electrolytic capacitors may require additional considerations.
Reliability: Film capacitors generally have longer lifespans and self-healing properties, while aluminum electrolytic capacitors require life calculations based on usage profiles.
Failure Modes: Film capacitors have better tolerance for overvoltage, while aluminum electrolytic capacitors are more prone to destructive failures under stress.
Cost: Aluminum electrolytic capacitors are more cost-effective upfront, but film capacitors may reduce additional circuit costs and offer greater long-term reliability.
Capacitor, Pros and Cons
Aluminum electrolytic capacitor (Al-Ecap)
Construction
Al-Ecap is composed of electrolyte impregnated paper layer sandwiched between two highly roughened metal foils (Fig.12). Grown directly onto the anode foil is a thin, very high quality oxide which acts as the dielectric. A well-grown oxide layer possesses excellent breakdown voltage characteristics (0.667-0.714 V/nm*15 ). An electrolyte/foil system acts as the cathode. The electrolyte is used as an electrode instead of a metal plate in order to maintain the integrity of the oxide dielectric via ion current *16 and provide good contact to the fragile oxide surface.
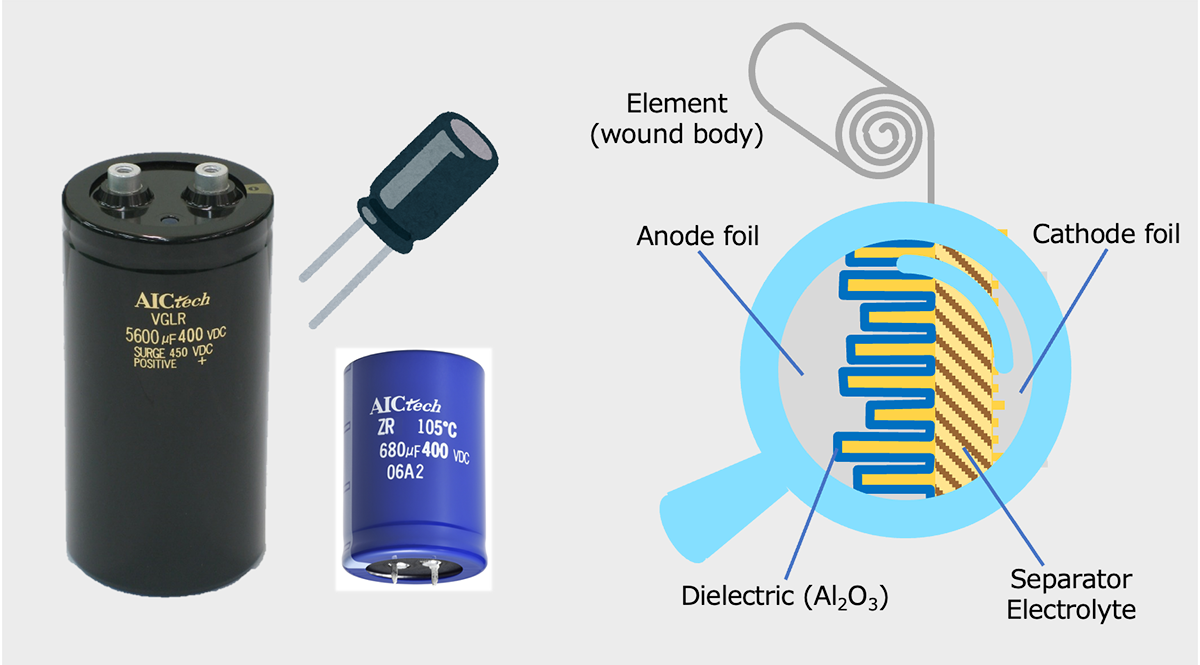
Outlooking and element structure of Al-Ecap
*15 A. Morley and D. Campbell, “Electrolytic capacitors -their fabrication and the interpretation of their operational behavior," Radio Electronic Engineering, vol. 43, pp. 421-429, Jul. 1973. [41]
*16 H. Ma and L. Wang, \Fault diagnosis and failure prediction of aluminum electrolytic capacitors in power electronic converters," in 31st Annual Conference of IEEE Industrial Electronics Society, 2005 (IECON 2005), 2005, pp. 842{847. [42]
Manufacturing process
Anode foil
The manufacturing process for Al-Ecap begins with a high-purity (~99.99%, at least 99% *17) aluminum metal foil (150 to 100 μm thick), which is the precursor for the anode foil. The anode foil is roughened by etching to form an electrode foil with a large surface area. However, if the anode foil contains even ppm levels of different metals such as Bi, Si, Mg, and Zn, the roughening process will be disturbed, so a high-purity aluminum foil with very few impurities is required for the anode foil. The surface of aluminum is also covered with a natural oxide layer about 5 nm thick when exposed to oxygen *18 . In the anode foil process, this oxide is removed by immersing the foil in a high-temperature sodium hydroxide solution or similar solution *19 .
*17 K. Arai, et. al., “Effect of trace-elements on etching of aluminum electrolytic capacitor foil," Journal of the Electrochemical Society, vol. 132, no. 7, pp. 1667{1671, 1985. [44]
*18 M. Saif, et. al., “Effect of native al2o3 on the elastic response of nanoscale al films," Acta Materialia, vol. 50, no. 11, pp. 2779{2786, 2002. [45]
*19 P. M. Deeley, “Electrolytic capacitors," The Cornell-Dubilier Electric Corporation, Tech. Rep., 1938. [46]
After removing the natural oxide layer on the surface, the aluminum foil is roughened by passing it through a strong acid solution at high temperature and applying a voltage (AC, DC, or both) between the solution and the foil *20. Specifically, numerous parallel hollow tunnels are formed perpendicular to the foil surface. These tunnels increase the surface area of the foil by as much as 100 times *21. The etched foil is then immersed in deionized water (DI) and nitric acid (HNO3) to remove impurities and residues.
*20 S. Parler, “Application guide, aluminum electrolytic capacitors,” Cornell-Dublier, Tech. Rep. [47]
*21 O. G. Palana, Engineering Chemistry. McGraw-Hill Education, 2009.[43]
The dielectric is an oxide on the surface of aluminum foil
The dielectric of Al-Ecap is an ultra-thin oxide on the surface of aluminum. Since the thin oxide layer is acting as the only dielectric in this system, the oxide quality is most important for the capacitor. This oxide is produced by anodic oxidation, also known as forming. The forming is an electrolytic passivation process *22. To grow an oxide from a metal foil, a voltage of approximately 135 to 200% of the final rated voltage of the capacitor is applied from a DC power supply with aluminum as the anode in a conductive aqueous solution *26. This causes aluminum ions to react with water to form an oxide (Al2O3), and the reaction in Equation (04) produces H2 *27. Specifically, the anodization process is performed by connecting the foil to the positive terminal of DC voltage source and rolling the foil into an aqueous electrolyte bath. The negative terminal is connected to the cathode rod placed in the electrolyte bath.

Electrolytes used in the forming process are chosen to be chemicals that do not dissolve the oxide, and the pH of the electrolyte is maintained at an appropriate level to control the porosity of the oxide. Neutral electrolytes (typically ammonium borate, phosphate, or tartrate) do not dissolve Al2O3 and can form dense, barrier oxide films *23, 24. Acidic electrolytes (typically sulfuric acid, but also oxalic acid and phosphoric acid) tend to dissolve some of the oxide layer as it grows tends to dissolve the oxide layer and can form a thicker, more porous layer *25. The growth rate of oxide is determined by the flow of Al+3 ions from the metal and O2- ions from the electrolyte *25. Since both ions flow from opposite directions, the formed oxide is grown at both the metal/oxide and oxide/electrolyte interfaces (Fig.13). As a result, the oxide is grown both outside and inside the metal surface. The speed at which these ions diffuse (the speed at which the oxide grows) is proportional to the current density (A/cm2)*27.
*22 Anodic oxide formation is also possible with valve metals such as niobium, tantalum, titanium, and silicon.
*23 A. Zagiel, et al., “Plating on anodized aluminum-the effect of the metal, the anion and the aluminum alloy," Electrochimica Acta, vol. 35, no. 6, pp. 1019-1030, Jun. 1990. [51]
*24 Tanaka, et al., The journal of the Surface Finishing Society of Japan 542-553 vol.69 12 2018
*25 J. O'Sullivan, “The morphology and mechanism of formation of porous anodic films on aluminum," in Proceedings of the Royal society of London. Series A, Mathematical and Physical Sciences, vol. 317, no. 1531, 1970, pp. 511-543. [52]
*26 S. Parler, “Application guide, aluminum electrolytic capacitors,” Cornell-Dublier, Tech. Rep. [47]
*27 G. E. Thompson, “Porous anodic alumina: Fabrication, characterization and applications," Thin Solid Films, vol. 297, no. 1-2, pp. 192{201, Apr. 1997. [53]
As mentioned earlier, the forming process, oxides start to form from both interfaces (Al2O3/Al and Al2O3/electrolyte). In the case of an anode foil with etched tunnels, this means that the oxide grows in both directions, in the tunneled pit holes and toward the aluminum metal (Fig.13) *28. This results in an oxide/metal interface with excellent adhesion and few defects that may affect the electrical properties of the oxide film. The thickness of the oxide is extremely uniform.
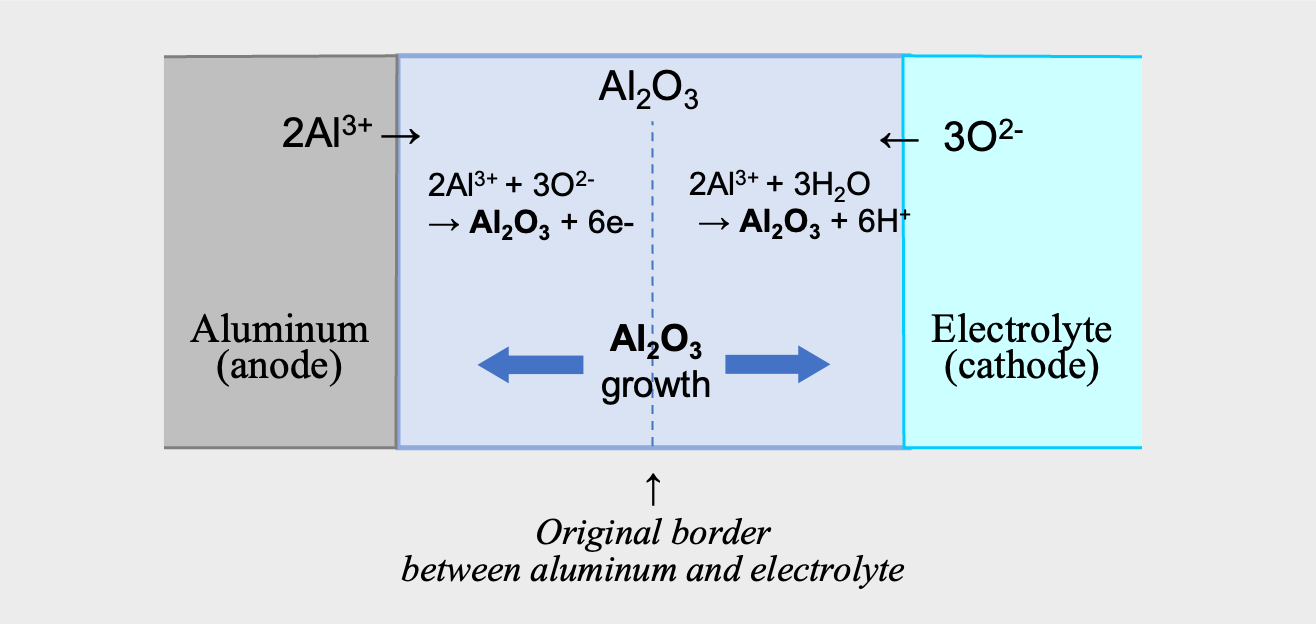
Schematic diagram of anodic oxide growth
*28 R. S. Timsit, W. G. Waddington, C. J. Humphreys, and J. L. Hutchison, “Structure of the al/al2o3 interface," Applied Physics Letters, vol. 46, no. 9, p. 830, 1985. [56]
During the forming process, the anodization proceeds so that a constant voltage is applied to any part of the etched aluminum foil (whether on the surface or inside the tunnel pit) *29. The resulting oxide film thickness is very uniform, and the uniformity of Al-Ecap's oxide film thickness is one of the reasons why Al-Ecap can operate at voltages closer (~80%) to the breakdown voltage (VBD) than other types of capacitors *30.
*29 A. Morley and D. Campbell, “Electrolytic capacitors -their fabrication and the interpretation of their operational behavior," Radio Electronic Engineering, vol. 43, pp. 421-429, Jul. 1973. [41]
*30 G. Terzulli and B. W. Peace, ”Film technology to replace electrolytic technology," AVX Corporation, Tech. Rep., Jul. 2005. [58]
As the current continues to flow, oxides are formed and the voltage increases. In actual forming process, however, there is a limiting voltage that depends on the type of anode metal, the type and concentration of the solute, and the current density. When the voltage reaches the limit value, the voltage does not increase even if current is applied, and no oxide is formed. In this case, various phenomena occur, such as the generation of oxygen gas at the anode, decomposition of the electrolyte, and electron avalanche destruction of the oxide. The lower the concentration of the solute in the electrolyte, the higher the limiting voltage, but even for aqueous electrolytes, the voltage is less than 1000V. Therefore, the maximum thickness of the oxide is about 1 μm.
Since the oxide layer grows inside the tunnels, the tunnels are partially occluded and the effective surface area of the foil is reduced. If the tunnel is too narrow, the oxide would fill the tunnel and capacitance will be greatly reduced. Tunnels with too large a diameter cannot increase the effective surface area of the foil, and therefore cannot increase.
For this reason, manufacturers optimize the tunnel diameter according to the required oxide thickness and carefully control the tunnel pit density and oxide film thickness in the aluminum foil to obtain high withstand voltage and large capacitance. In general, foils for low-voltage applications have thin oxide layers and small, dense tunnels, while foils for high-voltage applications have thicker oxide layers and larger tunnels *31.
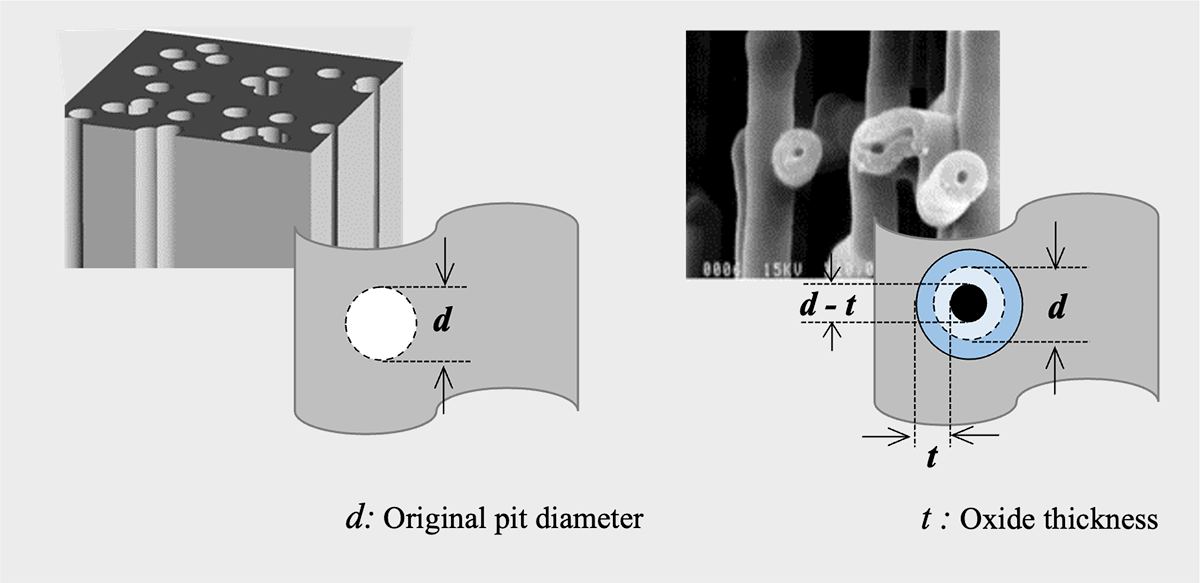
Schematic diagram of tunnel pit on aluminum foil (left), and oxides (right)
*31 S. Parler, “Application guide, aluminum electrolytic capacitors,” Cornell-Dublier, Tech. Rep. [47]
Electrolyte and Separator
An element wound with an anode foil, separator, and cathode foil is immersed in the electrolyte and the element is filled with the electrolyte using a vacuum/pressure cycle (also called impregnation). The electrolyte recipe is very important because the electrolyte greatly affects the equivalent series resistance, thermal stability, high breakdown voltage, and ability to repair defects during voltage operation of aluminum electrolytic capacitors. Specific electrolyte formulations vary from manufacturer to manufacturer, and most manufacturers have their own proprietary know-how.
In general, electrolytes are classified into two types: aqueous and non-aqueous. Aqueous electrolytes are based on aqueous boric acid or sodium borate solutions and add various alcohols or ketones to slow evaporation. Nonaqueous electrolytes have a very low water content and are usually composed of a weak acid (usually an organic or boric acid), a salt of the weak acid (usually ammonium or some other metal), and a solvent. Both types of electrolytes may also contain thickening agents or additives to change the pH (buffering agents), prevent the formation of H2 gas (degassing agents or gas adsorbers) *32, or passivate the Al or al2o3 surface *33.
*32 N. Helmold et. al., “Identification of missing or insufficient electrolyte constituents in failed aluminum electrolytic capacitors," in 24th Annual Capacitor and Resistor Technology Symposium (CARTS), 2004, pp. 122-127. [59]
*33 J. Stevens et. al., “The effects of electrolyte composition on the deformation characteristics of wet aluminum ICD capacitors," in The Capacitor and Resistor Technology Symposium (CARTS), 2006. [60]
The resistance of the electrolyte greatly affects the ESR of Al-Ecap. Capacitor manufacturers have focused on developing electrolytes with high water (H2O) content in order to obtain electrolytes with low resistance. Water in the electrolyte also has the effect of reforming the oxide film (Al2O3) through the reaction in Equation (05).
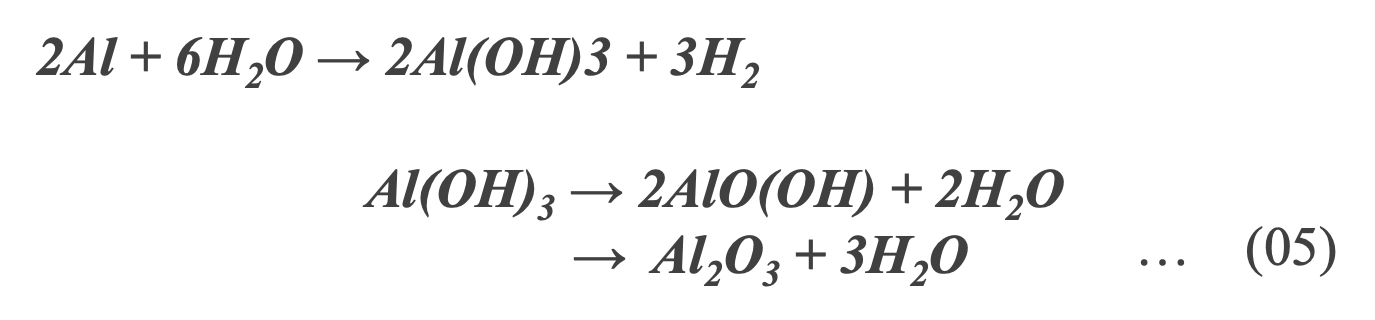
While water in the electrolyte has the effect of extending the life of the capacitor, the reaction in Equation (05) consumes H2O in the electrolyte and generates H2; the decrease in H2O leads to an larger ESR, and the generation of H2 leads to raise internal pressure. In other words, while the presence of H2O provides a high quality dielectric layer, it also reduces the life and characteristics of the capacitor.
Cathode foil
The aluminum foil used for the cathode foil has a thin oxide film (natural oxide film), which has capacitance. Therefore, the equivalent capacitance (Ceq) of Al-Ecap can be expressed as the capacitance when the anode foil capacitance (Ca) and the cathode foil capacitance (Cc) are connected in series using Equation (06).
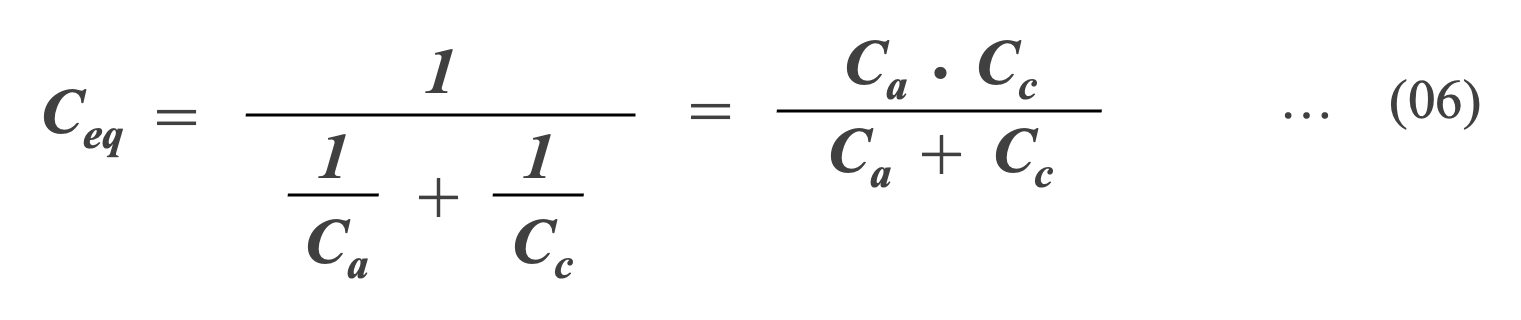
Equation (06) shows that the smaller capacitances connected in series affect the overall equivalent capacitance. If Cc is very small, the numerator in Equation (06) approaches zero, so Ca must be as large as possible. For a cathode capacitance 50 times that of the anode foil, the drop in Ceq is only 2%.
Al-Ecap has polarity
The polarity of Al-Ecap is due to the rectifying properties of the dielectric: when a reverse voltage is applied to Al-Ecap, an electrochemical reaction occurs that is opposite to the growth of the oxide. That is, the oxide is reduced back to aluminum metal. When the oxide is sufficiently reduced that the thin oxide layer can no longer electrically insulate the anode and cathode, the electrolytic capacitor will short circuit. The Joule heat generated by the short circuit vaporizes the electrolyte, increasing the internal pressure and causing gas to blow out of the seal. Applying a reverse voltage of only 1 to 1.5 V for about one second can produce enough gas to rupture the capacitor can.
Assembly
The Al-Ecap element consists of an anode foil, a separator impregnated with electrolyte, and a cathode foil. Aluminum ribbons (tabs) are cold-welded to the element and external terminals. The arrangement and number of tabs are key to the low resistance and low inductance of the Al-Ecap. The capacitor element is then encapsulated and sealed in an aluminum case.
Because the electrolyte generates H2 gas when a voltage is applied to the capacitor, a pressure relief vent is installed in the aluminum case and is designed to relieve the internal pressure, which is usually greater than 5 atmospheres. Pressure relief vents are available in the form of rubber bungs or gaskets that are pushed out by the internal pressure, or with a mold slit at the top.
After being sealed in an aluminum case, the capacitor is connected to a power supply and slowly raised to a specified voltage under a defined ambient temperature. This process is called aging and allows oxide to grow and repair in areas where oxide formation is inadequate (such as slit foil edges and cracks) and debug capacitors with defects that occurred during the manufacturing process.
Metalized Film Capacitor (MF-cap)
The technology of using plastic film in capacitors has been applied since the 1950s, and foil-electrode polypropylene capacitors, which use thick metal foil for electrodes, have been in practical use since the 1970s*34. However, this type of capacitor has the disadvantage of poor lifetime characteristics because local inhomogeneities and defects in the dielectric film can lead to major failures.
*34 J. Ho, et. al., “Historical introduction to capacitor technology,“ IEEE Electrical Insulation Magazine, vol. 26, no. 1, pp. 20-25, 2010. [61]
The MF-cap is applied metallization technology to form an ultrathin metal layer on the film surface. The MF-cap is applied metallization technology to form an ultrathin metal layer on the film surface. MF-cap makes possible extend lifetime performance and downsize.
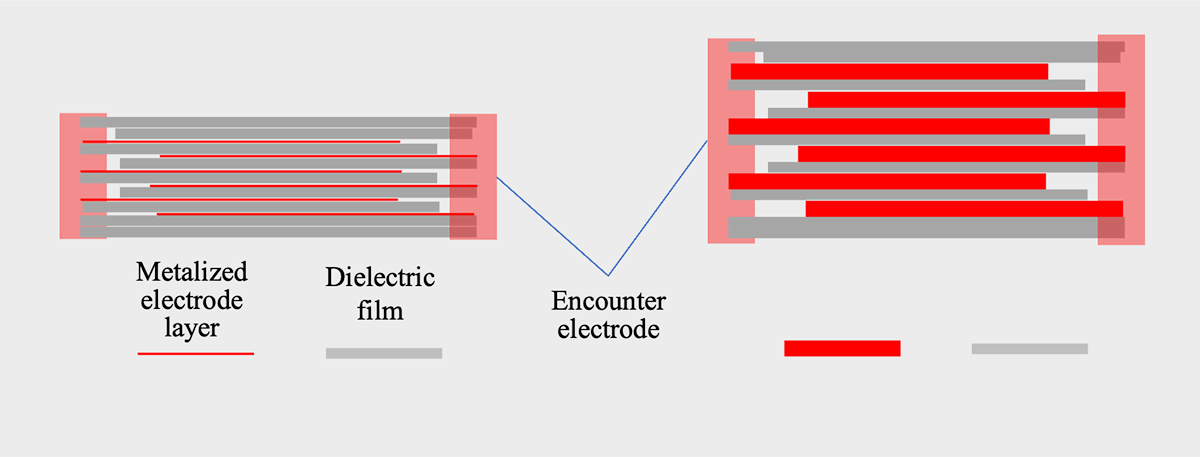
The cross section schematic diagram of MF-cap (left) and foil-electrode type capacitor (right)
Types and Features of Dielectric Films
The most common dielectric films that are used in the industry are mainly polypropylene (PP) or polyethylene terephthalate (PET). In special applications, dielectrics such as polyethylene naphthalene or polyphenylene sulfide are used for high-temperature operating conditions (up to 150°C).
PET film capacitors have higher capacitance per volume than PP film capacitors due to their high permittivity and availability in thinner film around 1μm. They also have a better mechanical resistance and a slightly higher exploitation temperature than PP film capacitors, with operating temperatures up to 125°C. The negative point is that the loss factor is approximately twenty times larger, which means higher temperature elevation for the same rated power (Table 3).
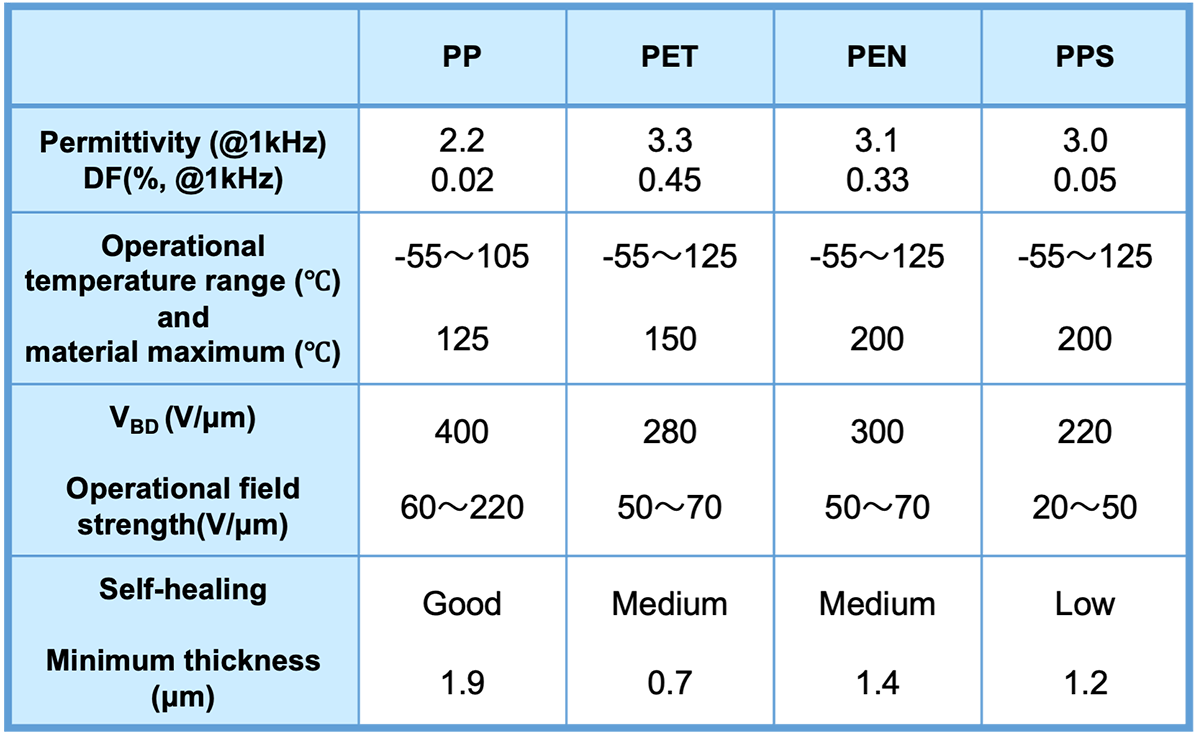
Polypropylene type MF-cap
PP film has superior electrical characteristics. PP film capacitors exhibit very little capacitance change over time with an applied voltage, making them ideal for applications where a stable level of capacitance is needed.
The capacitance and ESR of MF-caps are extremely stable with respect to changes in temperature and frequency, and the loss factor is lower than that of any other film capacitor, making them suitable for high-frequency applications*35. Also, the PP film material absorbs less moisture than PET film*36 *37、PP MF-cap is often used in applications that require high reliability, such as DC links in inverters and power supply filters.
PP film, called BOPP, is manufactured by biaxially oriented stretching process*38. BOPP made by this process has a cost advantage over other films. However, BOPP MF-cap also tends to suffer faster degradation in capacitance at higher temperatures. In addition, the phase transition of the polymer reduces insulation properties, resulting in a relatively low operating temperature. The category upper limit temperature for ordinary BOPP type MF-cap is 105°C.
*35 N. Henze and J. Liu, “Reliability considerations of low-power grid-tied inverter for photovoltaic application," in 24th European Photovoltaic Solar Energy Conference and Exhibition, Hamburg, Germany, Sep. 2009, pp. 21-25. [68]
*36 Gallay, R. “Metallized Film Capacitor Lifetime Evaluation and Failure Mode Analysis.” Proceedings of the CAS-CERN Accelerator School: Power Converters: pp. 45-56. May 2014. [1]
*37 Vishay application notes. "Characteristics and Definitions used for Film Capacitors." Document No. 28147. 2008. [3]
*38 M. Rabu and G. Picci, “Status quo and future prospects for metallized polypropylene energy storage capacitors," IEEE Transactions on Plasma Science, vol. 30, no. 5, pp. 1939-1942, Oct. 2002. [69]
In recent years, PP polymers with higher voltage resistance and higher melting points have been developed and commercialized through improvements such as tacticity *39 and higher purity of PP polymers. In other words, crystalline PP polymer with a high melting point called isotactic polypropylene (iPP) (Fig.16) is used. By removing impurities such as catalyst residues, PP polymers with excellent properties have been obtained. Nowadays, PP-type MF-cap, which can handle 125°C, has also been introduced.
*39 Polypropylene has a methyl group attached to the double bond, and its structure changes depending on the steric configuration of the methyl group. This steric relative arrangement of substituents on the main chain of a polymer is called stereo-regularity (or “tacticity”).
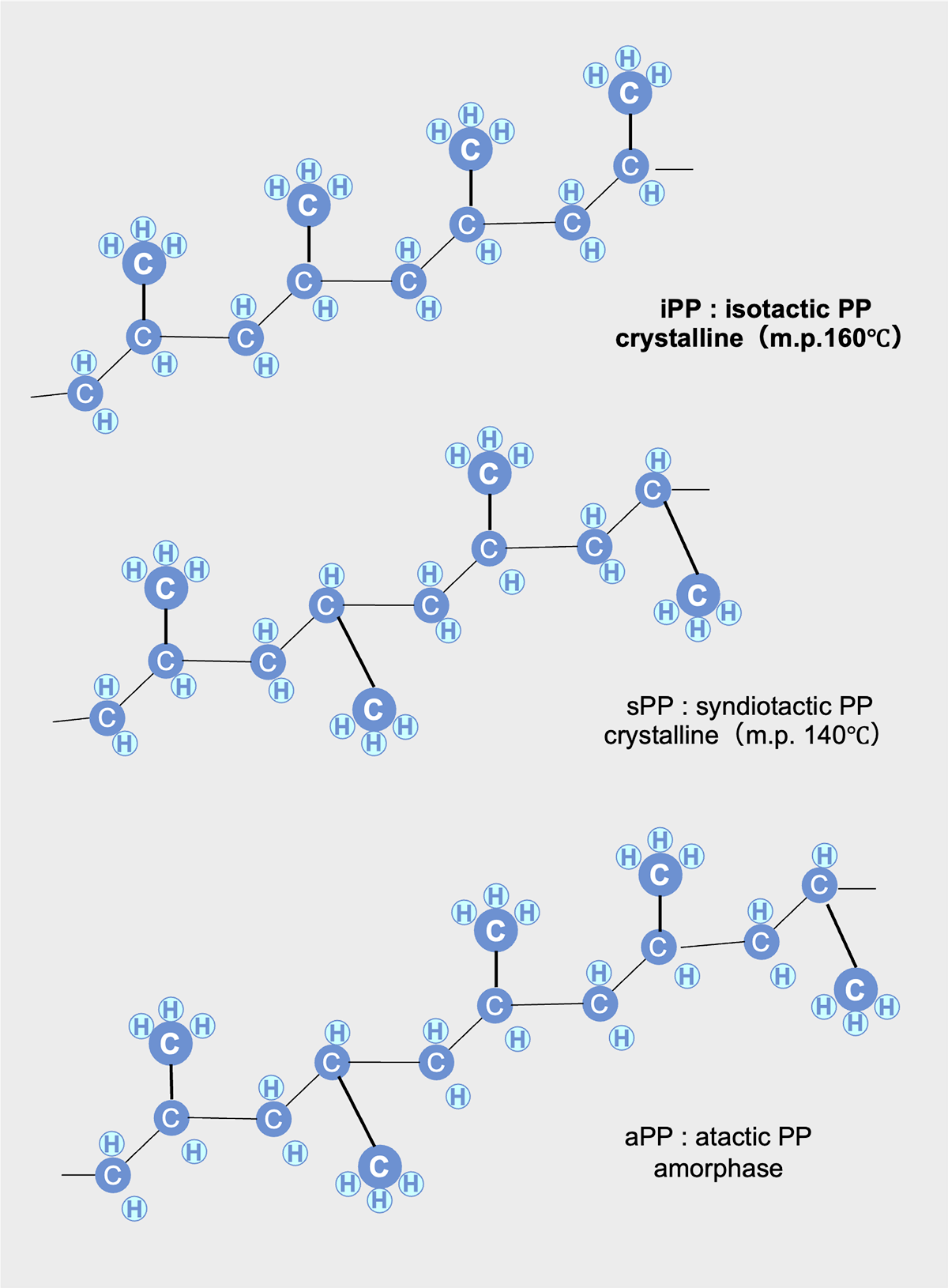
Polypropylene (PP) structures
MF-cap structure and manufacturing process
MF-caps consist of a dielectric plastic film 1-10μm in thickness which is metallized on both sides or one side of the film*40. The electrodes are usually Al and Zn in pure or alloyed states *41, in thickness of 20-100nm *42. Corona treatment on the film surface beforehand can improve the adhesion between the metalized electrode layer and the film*43. Two layers of film are wound together as tightly as possible to avoid any air voids (Fig. 20). Electrical connections are made by end spraying a metal (typically Zn) the exposed edges of the roll. The final electrical connection is made by soldering or welding a tab or lead wires onto the end-sprayed metal.
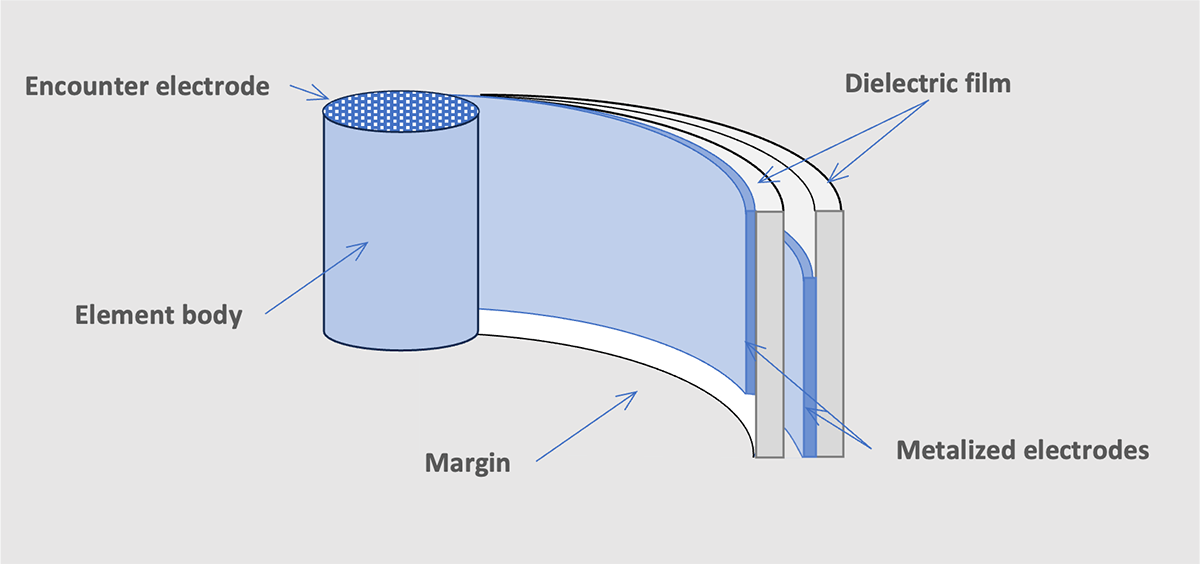
Wound type element of MF-cap
*40 M. El-Husseini, et al. “Effect of the geometry on the aging of metalized polypropylene film capacitors," in IEEE 32nd Annual Power Electronics Specialists Conference, 2001 (PESC 2001), 2001, pp. 2061-2066. [62]
*41 L. Hua, et al. “Study on metallized film capacitor and its voltage maintaining performance," IEEE Transactions on Magnetics, vol. 45, no. 1, pp. 327-330, 2009. [63]
*42 J. Zhao and F. Liu, ”Reliability assessment of the metallized film capacitors from degradation data," Microelectronics and Reliability, vol. 47, no. 2-3, pp. 434-436, Feb.2007. [65]
*43 It is said that pin poles with an area of 5 to 8 mm3 exist in isolated areas. C. W. Reed and S. W. Cichanowskil, “The fundamentals of aging in hv polymer film capacitors," IEEE Transactions on Dielectrics and Electrical Insulation, vol. 1, no. 5, pp. 904-922, 1994. [64]
Segmented metallization technology
Poor lifetime characteristics as local defect points in the dielectric film would quickly lead to local, then global, failure. Poor lifetime performance of film capacitors was improved by the metallization technology which form nanometer thickness electrode. For example, MF-cap has metallization layers which are segmented into larger electrode areas separated by thin metallized current gates*44, 45. These gates act as fuses which will fail before the failure of the entire capacitor. In other words, larger patches of metal electrode are separated by much thinner current gates. For normal clearing behavior, the current gates are unaffected. However, for very large failures, the current gates should readily evaporate, isolating the failed metallized electrode segment before it can affect neighboring segments.*46 (Fig.18).
*44 J. B. Ennis, et al. “Recent advances in high voltage, high energy capacitor technology," in IEEE International Pulsed Power Plasma Science Conference, 2007 (PPPS 2007), 2007, pp. 282-285. [72]
*45 D. Xin, et al. ”Influence factors for the self-healing of metallized polypropylene capacitors," in Annual Report Conference on Electrical Insulation and Dielectric Phenomena, 2000, pp. 461-465. [73]
*46 A. Gully, “Failure mechanisms in film-based power capacitors," in Seventh International Conference Dielectric Materials, Measurements and Applications, no. 430, 1996, pp. 358-363. [75]
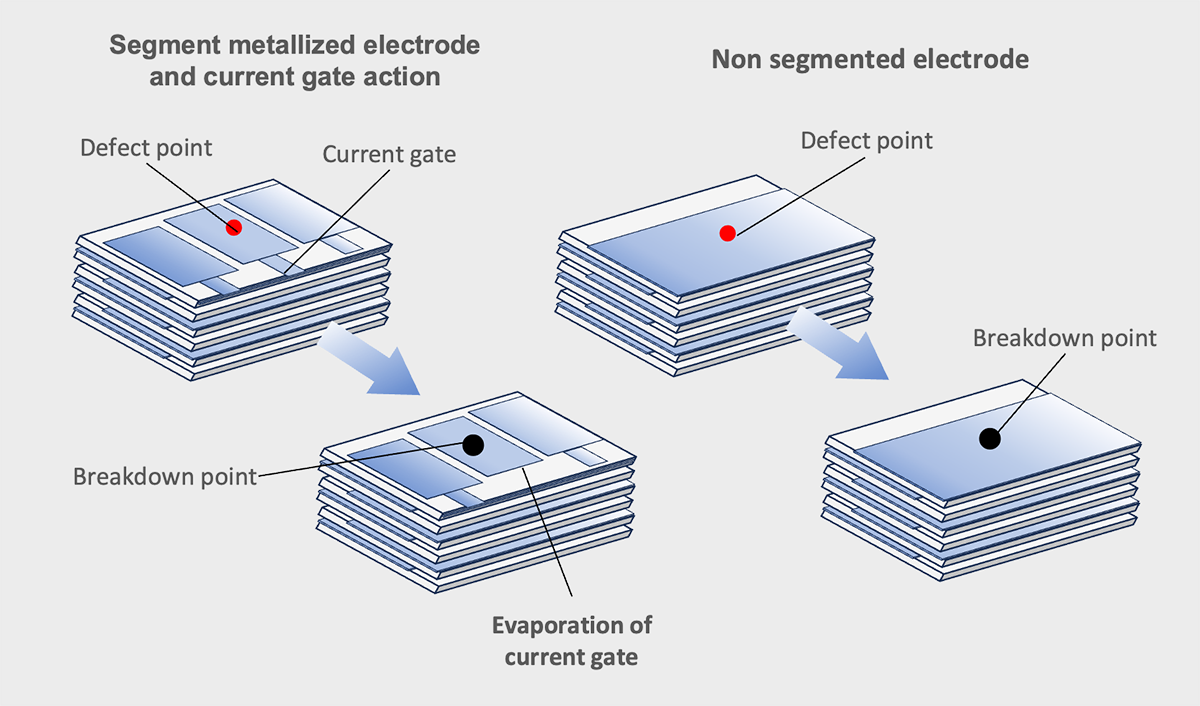
Segmented metallization technology
The electrodes that collect the metalized electrodes are formed by metal spray technology. At this process, melt metals such as aluminum and zinc by arc discharge and blow them onto the film windings with compressed air. It is important to form a dense layer by properly adjusting the air volume and velocity, distance, and time of the blowing (Fig.19).
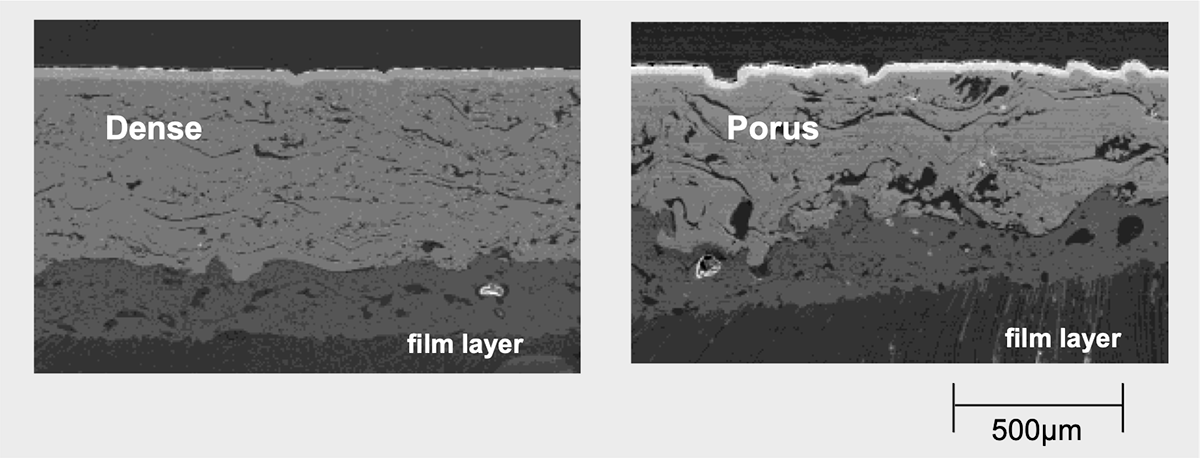
Cross-section of encounter electrode layer of MF-cap
The degradation of metallized film capacitors is a concern in applications or production process exposed to high humidity environments. . The metallized electrode layer in MF-cap is very thin, typically less than 50 nm, which is susceptible to corrosion due to the penetrate of atmospheric moisture. In the case of cylindrical shape elements, The normal protective surface oxide formation may be comparable in thickness to that of the metal film. Corrosion usually progresses from the ends of the capacitor cylinder to the middle, related to the ingress of atmospheric moisture. Corrosion of metallized electrodes leads to an uneven distribution of current, which causes localized heating and eventually leads to catastrophic failure. Details will be explained in section 3.3 (3).
Multi Layer Ceramic Capacitor (MLCC)
MLCCs are currently not used in high power electronics applications due to cost considerations. However, their price has been rapidly decreasing and, in the near future, they may begin to be utilized in inverter systems. For now, they are mostly used in low power consumer electronics.
MLCCs consist of repeating layers of ceramic sandwiched by metal electrodes (Fig. 23). A wide range of ceramics may be used as the dielectric medium with the most popular being variations of barium titanate (BaTiO3). The ceramic is usually created via sintering of a “green sheet", a ceramic powder or slurry in a carrier. Since the electrodes are co-fired with the ceramic powder, the electrode is limited to materials with a higher melting temperature than the sintering temperature of the ceramic (~1100-1700K, depending on the ceramic).
Metal electrodes have been traditionally composed of precious metals (usually a 85% silver/15% palladium alloy). In order to decrease device cost in the face of rising palladium costs, many manufacturers have been moving towards base metal electrodes (usually Ni with Cu terminations).
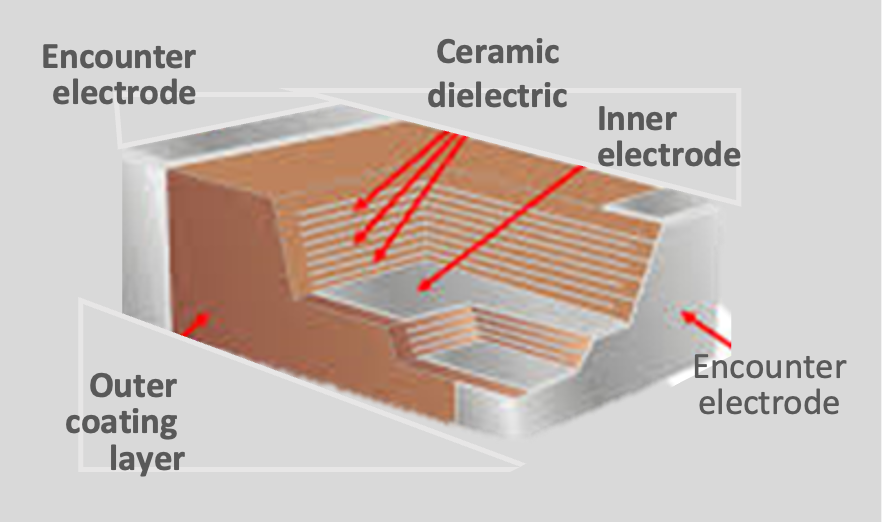
MLCC structure
Although progress towards base metal electrode MLCCs have been progressing rapidly, there are still manufacturing issues to overcome. Since the Ni electrodes require a reducing environment during sintering to avoid oxidation, oxygen vacancies are created in the ceramic. It is generally believed that vacancy ordering along grain boundaries eventually leads to a large, irreversible capacitance degradation in humid environments. It has also been postulated that due to humid environments, moisture may penetrate cracks in MLCCs and dissolve ionic impurities to form conductive bridges that decrease capacitance.
MLCCs have high operating temperatures with good reliability, however they suffer from poor temperature drift and stability. They also possess high dielectric constants, but poor VBD due to any remaining porosity after the sintering process. At present, MLCCs are currently too costly to be used for high power electronic systems at the present, there are many challenges for MLCC to compete with Al-Ecap and MF-cap in this application.
Application Case Studies
Capacitors are integral components in various power conversion applications, each serving specific roles to ensure optimal performance and reliability. Here's an overview of their applications:
Motor Drives: Capacitors, particularly aluminum electrolytic types, are employed in motor drives to filter ripple currents and stabilize inverter operations. They act as energy buffers, ensuring smooth motor control across a range of applications, from household appliances to industrial machinery.
Renewable Energy Systems: In solar and wind power generation, capacitors function as DC link components, smoothing voltage fluctuations and enhancing power conversion efficiency. Their reliability is crucial for the long-term stability of renewable energy inverters.
Servo Drivers: These systems utilize capacitors to manage energy exchange during motor operations, ensuring precise control of speed and torque. Aluminum electrolytic capacitors are commonly used to filter high-frequency components and maintain stable inverter performance.
Switching Mode Power Supplies (SMPS): Capacitors in SMPS configurations filter input and output voltages, contributing to compact, efficient power supplies with low power consumption. They are essential for stabilizing voltage and reducing electromagnetic interference.
Pulsed Power Supplies: In applications requiring instantaneous high power, such as X-ray generators and welding machines, capacitors serve as energy buffers, delivering rapid energy discharge. Their capacitance directly influences the power supply's ability to generate high-energy pulses.
Uninterruptible Power Supplies (UPS): Capacitors in UPS systems provide immediate power during outages, bridging the gap until backup systems activate. They also filter voltage spikes, protecting sensitive equipment from power disturbances.
Traction Control Systems: In electric railcars and vehicles, capacitors manage energy flow within inverters, ensuring efficient motor control and braking. They handle significant ripple currents and voltage fluctuations inherent in traction applications.
For a more in-depth exploration of capacitor applications in power electronics, including detailed case studies and technical insights, visit AIC tech Inc.'s comprehensive article:
Essential characteristics of capacitors
Capacitance
Capacitance is a fundamental property of capacitors, representing their ability to store electrical charge. It is defined as the ratio of the electric charge (Q) stored on the capacitor's plates to the voltage (V) across them, expressed by the formula C = Q/V. The capacitance value depends on factors such as the surface area of the plates, the distance between them, and the dielectric material used.
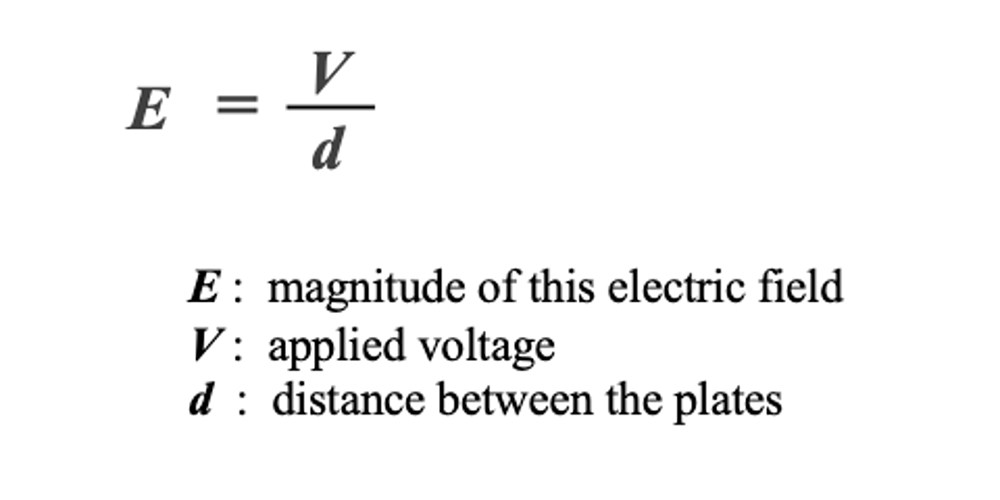
In practical applications, capacitance is influenced by environmental conditions like temperature and frequency, which can cause variations in performance. Understanding these dependencies is crucial for selecting the appropriate capacitor type to ensure optimal functionality in electronic circuits.
What is a large capacitance capacitor?
Although there is no clear definition of a large capacitance capacitor, we specialize in large capacitance capacitors for power electronics. So, what kind of capacitor is a large capacitance capacitor?
A capacitor stores an electric charge on an electrode. The larger the area of the electrode, the more electric charge can be stored. The two electrodes accumulate positive and negative electric charges, respectively, and the electric charges attract each other. The closer the electrodes are to each other, the stronger the force of attraction, so much electric charge is accumulated.
Also, as explained in section 1.2, an insulating material called dielectric is sandwiched between the electrode plates. Depending on the type of dielectric, the ability to store electric charge varies, and the index of that ability is called the permittivity. The above can be expressed in the following equation and diagram:


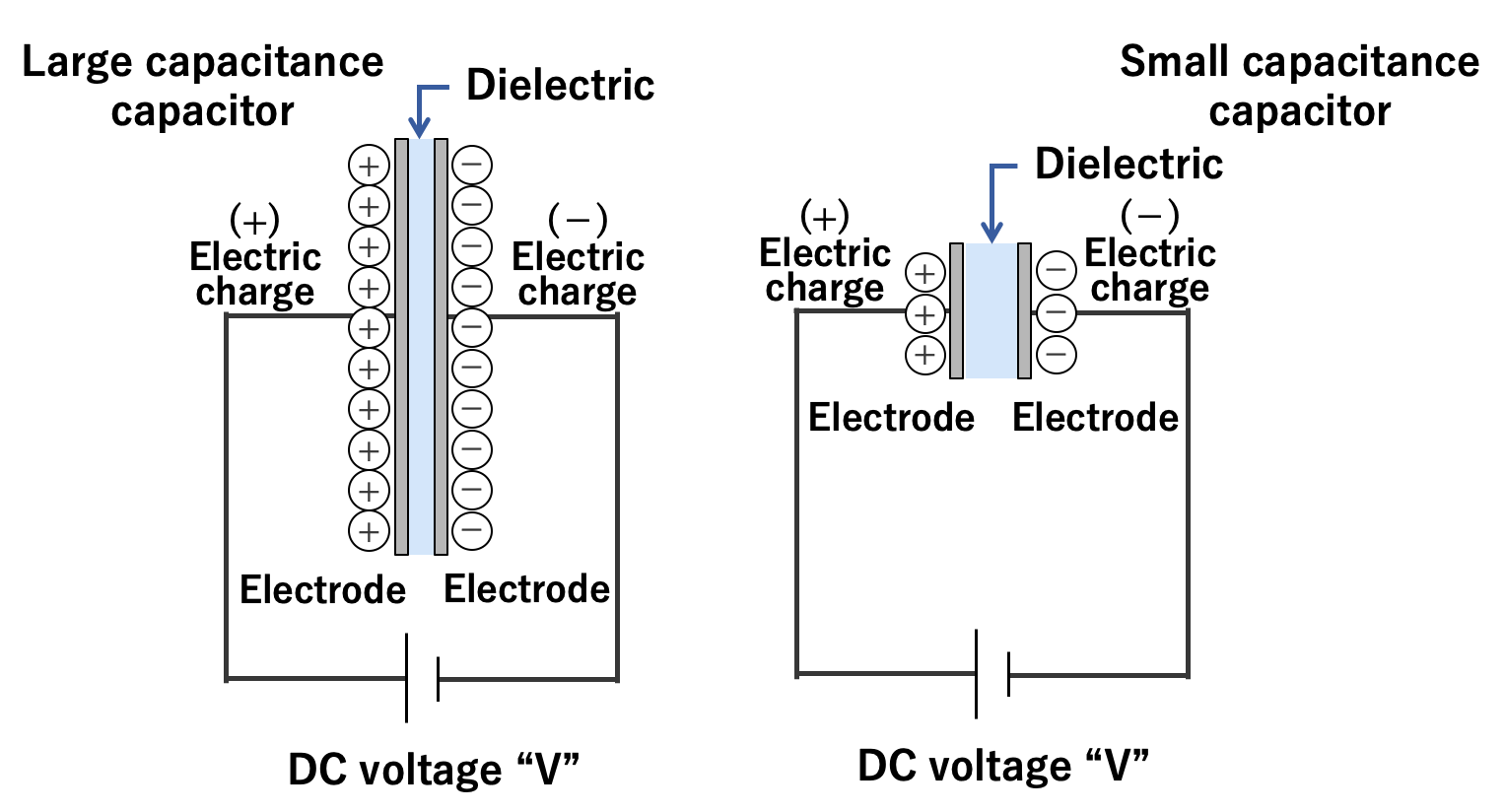
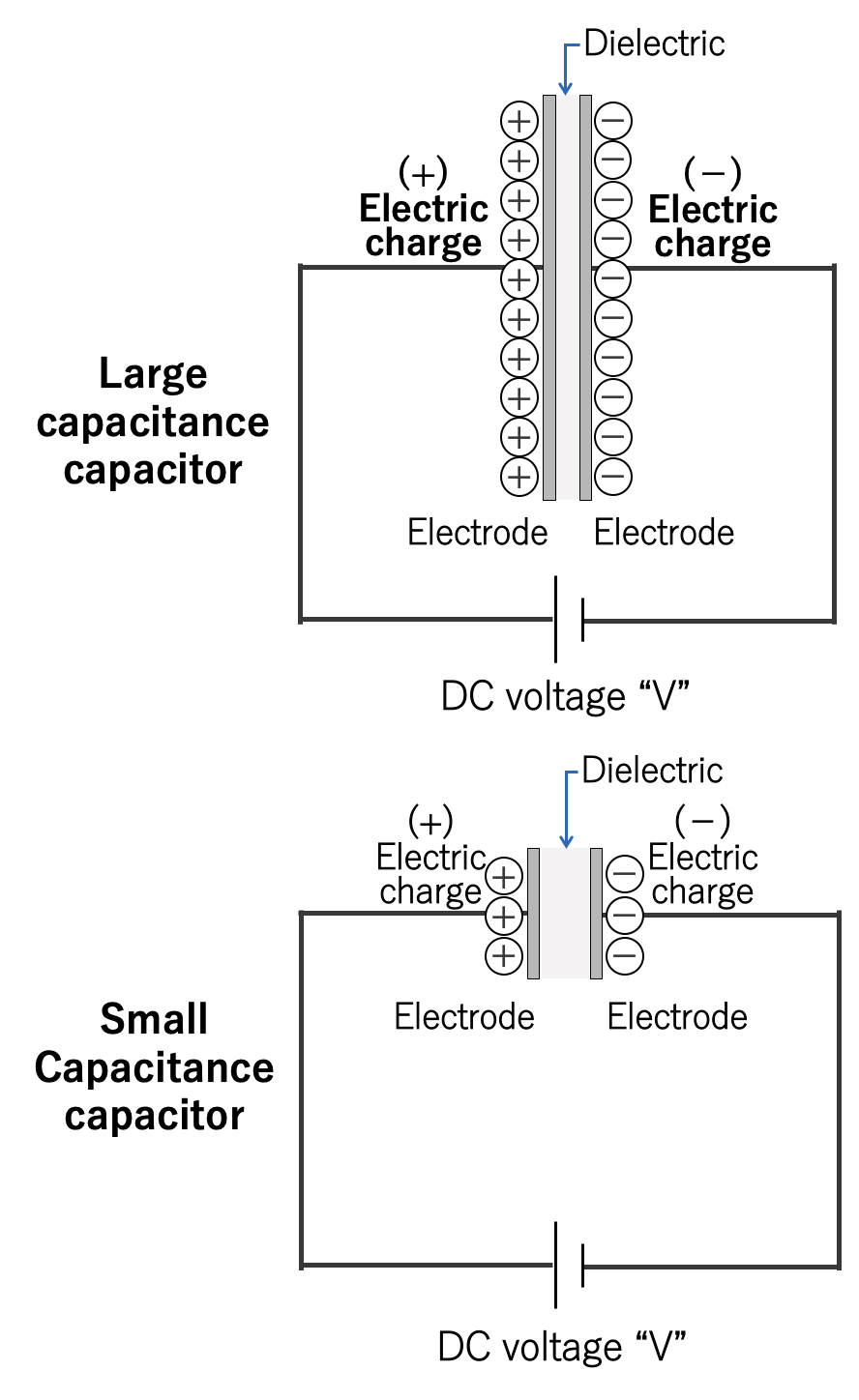
Also, as explained in section 1.2, the capacitance is the electric charge (Q) accumulated on the electrode divided by the applied voltage (V). If rewriting this equation, we can understand that as the voltage applied to the capacitor increases, the amount of electric charge increases.
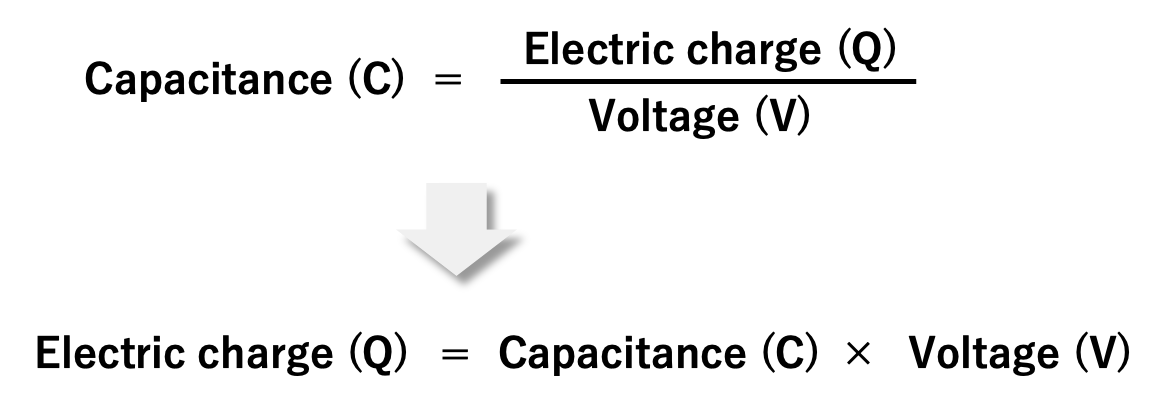
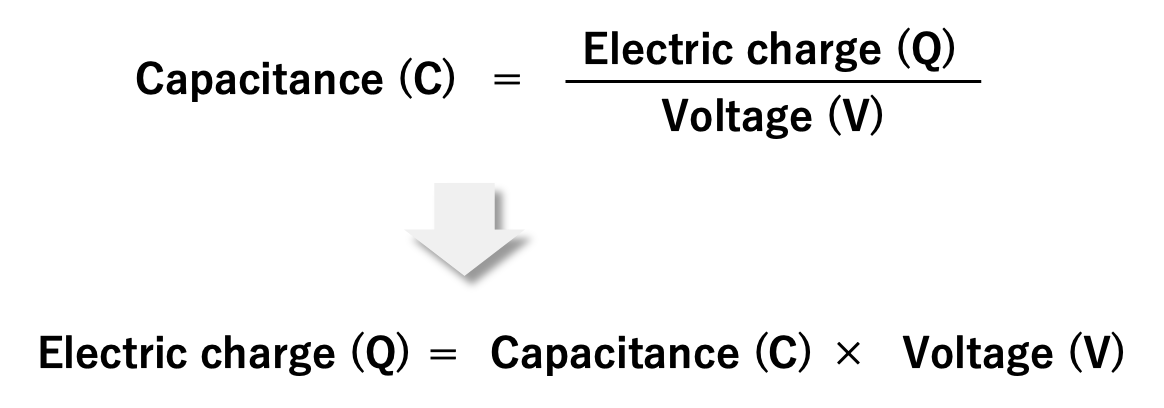
What are large capacitance capacitors?
The capacitance and voltage rating ranges of the four types of capacitors explained in Chapter 2 are shown in the figure. Capacitors cover an extensive range of capacitance, from a minuscule one nano farad (1 nF: one billionth of a farad) to a battery-like 1000 farads (F).
There is no precise definition for a large capacitance capacitor, but if we consider a large capacitance capacitor to be a capacitor with a capacitance of 47 to 100 microfarads (μF) or more, which is often used in the power supply circuits of electronic equipment, then electric double-layer capacitors, most aluminum electrolytic capacitors, and film capacitors of 1500 V or less can be considered large capacitance capacitors.
Impedance
Impedance is an essential parameter in capacitors, representing their opposition to alternating current (AC) flow. It is determined by the combination of resistance (R), capacitive reactance (Xc), and inductive reactance (XL), and varies with frequency. In capacitors, impedance decreases with increasing frequency up to a point, after which inductive effects cause it to rise. Key components influencing impedance include Equivalent Series Resistance (ESR) and Equivalent Series Inductance (ESL). ESR accounts for resistive losses, while ESL represents inductive properties inherent in the capacitor's construction. Understanding these factors is essential for selecting capacitors that meet specific performance requirements in electronic circuits.
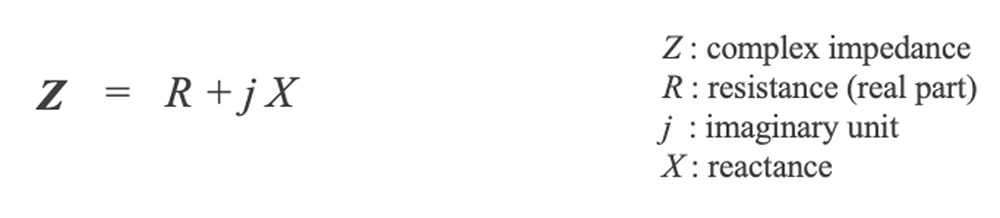
Leakage current
Leakage current and insulation resistance are key parameters that describe a capacitor's insulation properties. For film and ceramic capacitors, which exhibit very low leakage current, insulation resistance (Riso) is the primary measure. In contrast, for aluminum electrolytic capacitors with higher leakage currents, leakage current (ileak) is used as the defining parameter. These two properties are interconnected and can be expressed by a simple equation, highlighting their importance in evaluating a capacitor's performance and reliability.

Capacitor failures
Failure modes and mechanisms
Capacitor failures can be categorized into two main types:
Catastrophic Failures: These involve a complete loss of function, such as open or short circuits. Such failures can lead to severe consequences, including enclosure explosions, smoke, ignition, harm to other electrical components, or leakage of liquid or gas from within the capacitor.
Degradation Failures: These are characterized by a decline in performance parameters, such as increased leakage current, elevated Equivalent Series Resistance (ESR), or reduced capacitance. The specific parameters and their acceptable limits can vary among manufacturers.
The failure mechanisms leading to these modes can differ based on the capacitor type:
Aluminum Electrolytic Capacitors (Al-Ecap): Common failure mechanisms include electrolyte evaporation, dielectric breakdown, and corrosion, which can result in increased ESR, reduced capacitance, or complete failure.
Metalized Film Capacitors (MF-cap): Failures often stem from dielectric degradation, electrode oxidation, or film delamination, leading to capacitance loss or open circuits.
Multilayer Ceramic Capacitors (MLCC): Susceptible to mechanical stress, thermal cycling, and dielectric breakdown, MLCCs may experience cracking, capacitance loss, or short circuits.
Understanding these failure modes and mechanisms is vital for selecting the appropriate capacitor type and implementing effective design strategies to enhance the reliability and longevity of electronic systems.
Lifetime estimation
Estimating the lifetime of capacitors is essential for ensuring the reliability and longevity of electronic systems. The failure rate of capacitors typically follows a "bathtub curve," comprising three distinct phases:
Infant Mortality Phase: Characterized by a high initial failure rate due to manufacturing defects or early-life weaknesses.
Random Failure Phase: A period of relatively constant, low failure rates during the majority of the capacitor's operational life.
Wear-Out Phase: Marked by an increasing failure rate as the capacitor approaches the end of its useful life due to material degradation and other aging factors.
Key factors influencing capacitor lifespan include:
Operating Temperature: Elevated temperatures accelerate chemical reactions within the capacitor, leading to faster degradation.
Applied Voltage: Operating near or above the rated voltage can stress the dielectric material, reducing lifespan.
Ripple Current: High ripple currents generate additional heat, contributing to thermal stress and accelerated aging.
Manufacturers often provide lifetime estimation formulas that account for these variables, enabling engineers to predict capacitor longevity under specific operating conditions. By carefully considering these factors and selecting capacitors with appropriate ratings, designers can enhance the durability and performance of electronic systems.
Case studies
Understanding common failure modes and their causes is crucial for effective troubleshooting and prevention. This article presents 15 practical case studies of capacitor failures across different applications, offering insights into identifying problems and implementing appropriate solutions.
Explore the full article below to enhance your knowledge of capacitor troubleshooting and ensure the longevity of your electronic systems.
The future of large capacitance capacitors
[ Miniaturization ]
A large capacitance capacitor can be made by increasing the area of the electrodes and increasing the size of the capacitor. However, the use of large capacitors makes electronic devices larger and heavier, which leads to higher costs. For this reason, the miniaturization of large capacitance capacitors has always been a concern for customers and the most important task for capacitor manufacturers.
We have achieved the miniaturization of capacitors by improving electrode materials and processing technology. We are developing and improving materials and processing technologies, such as increasing the surface area of the anode aluminum electrode foil in aluminum electrolytic capacitors and using thinner films as dielectrics in film capacitors.
[ Responding to the evolution to power semiconductors ]
In recent years, power semiconductors have evolved greatly in power electronics, where large capacitance capacitors are used, and devices have become more efficient and smaller. Capacitors for these applications are required not only to have a small size and large capacitance but also to have improved heat resistance and longer life.
In addition to the technologies we have cultivated in miniaturization, we are pursuing breakthroughs in large capacitance capacitors by developing electrolyte solution and film materials and improving the capacitors' structure.
Conclusion
Capacitors (C), along with resistors (R) and coils (L), are the three most essential passive components in electronic circuits. In electronic circuits, attention is focused on semiconductors, but without passive components, semiconductors would not work. In particular, capacitors are indispensable partners for semiconductors that operate on direct current.
This time, we have explained the basics of capacitors and their capacitance. We hope you have become familiar with capacitors.
As mentioned earlier, large capacitance capacitors include electric double-layer capacitors, aluminum electrolytic capacitors, and film capacitors, and we have a full lineup of all of these. However, the performance, size, and price of each large capacitance capacitor have advantages and disadvantages. For this reason, we offer solutions for your applications. Next time, we will explain the applications and reliability of capacitors. We hope you find this column useful.
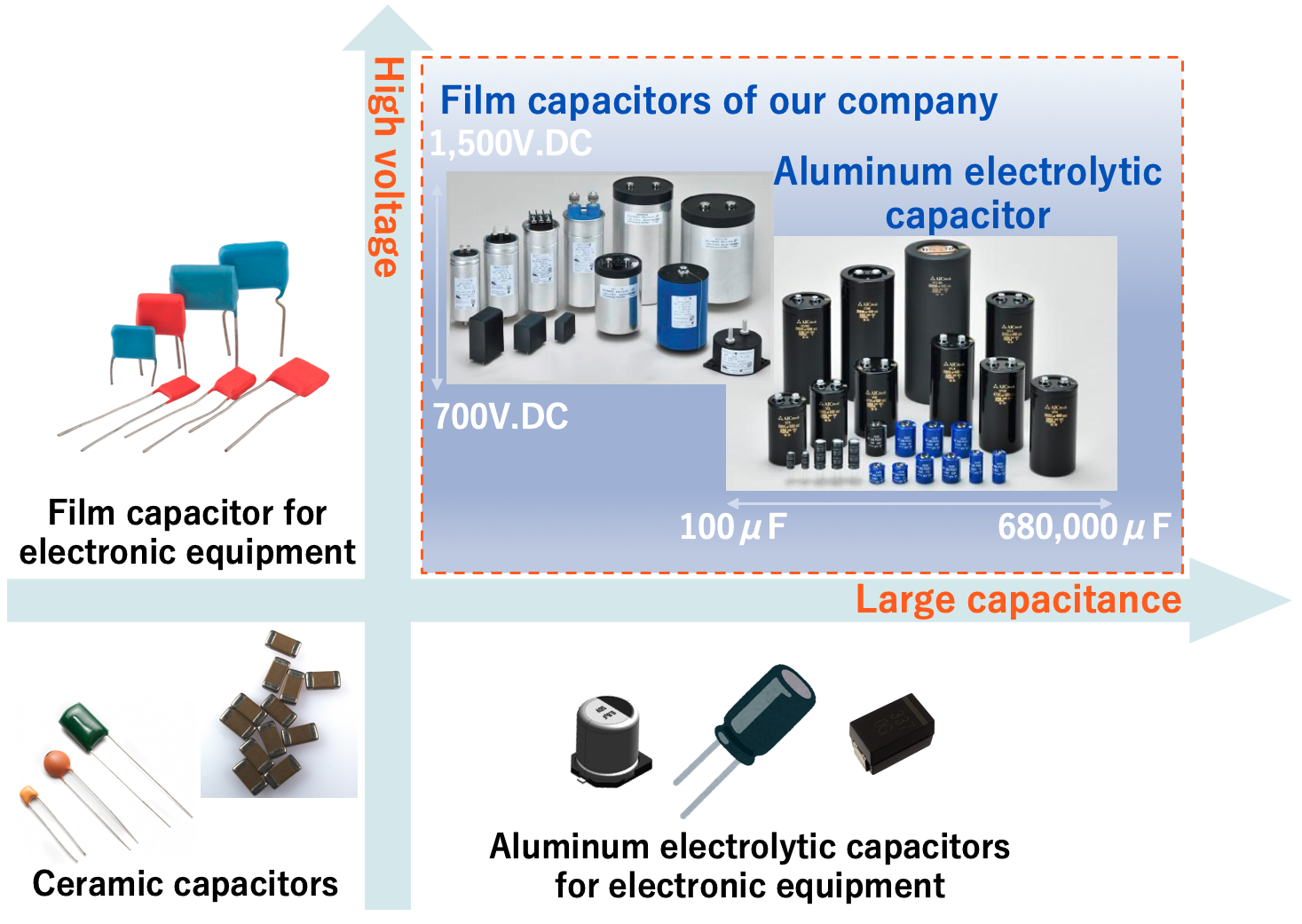
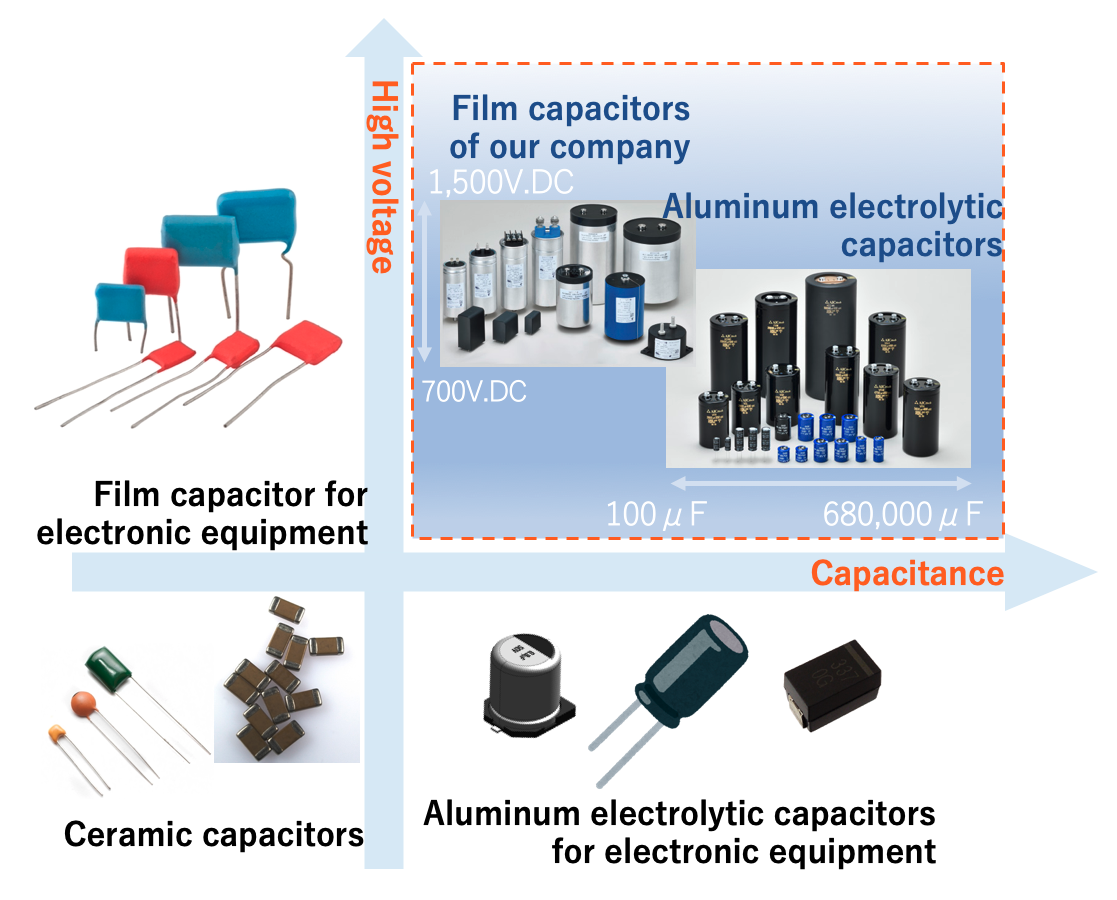
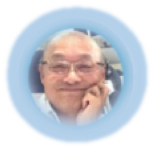
Editorial supervision/Kazuyuki Iida
General Advisor, AIC tech Inc.
Born in the Tokyo area in 1956
M.S. of Sc, Sophia University, Tokyo, Japan. 1982
Over 35 years experience with knowledge on capacitor technology, i.e. R&D for high-performance capacitor and its materials, marketing activities at Hitachi Chemical Co, Ltd. and Hitachi AIC Inc. and Contributed articles on capacitors to public relations magazines, trade journals, and various handbooks.
Instructor of capacitor technology at the Technical Training Institute of Hitachi, Ltd. from 2005 to 2015.
General advisor to AIC tech Inc. from 2020.
- "Tantalum Electrolytic Capacitor"
The Electrochemical Society of Japan (ed.) Maruzen Handbook of Electrochemistry, 5th Edition, Chapter 15, Capacitors, Section 15.2.4 b (1998) - "Development Trend and Material Technology of Tantalum-Niobium Capacitors"
Technical Information Association of Japan Seminar June 2008 - Lead-Free Surface Mount Film Capacitors MMX-EC, MML-EC Series
Hitachi Chemical Technical ReportNo. 48. Product Introduction 2007 - "Film Capacitors for Electronic Devices"
Maruzen Capacitor Handbook, 5th Edition, Chapter 5, Film Capacitors, Section 5.2 (2009). - "Film capacitor MLC series for new energy"
Shinkobe Electric Co., Ltd. Shinkobe Technical Report Np. 22 (2012).
PDF Download